Combined type demoulding method for fusion in X-ray fluorescence analysis of iron oxide ore
A technology for fluorescence analysis and iron oxide ore, which is applied in the preparation of test samples, etc., can solve the problems of long release time, reduced production efficiency, increased operating costs, etc.
- Summary
- Abstract
- Description
- Claims
- Application Information
AI Technical Summary
Problems solved by technology
Method used
Examples
Embodiment 1
[0016] ①Put 6g of anhydrous lithium tetraborate lithium metaborate mixed flux, 0.5g of cobalt powder, 0.5g of sample and 0.3g of lithium nitrate into the yellow platinum crucible, then add 1ml of lithium bromide solution with a mass concentration of 27%;
[0017] ②After the first heat stage (time 180 seconds, temperature 600°C), second heat stage (time 180 seconds, temperature 1100°C), enter the melting stage (time 240 seconds, temperature 1100°C, swing speed 6 times / second), add 0.015g of potassium iodide during the 180-200 seconds of the melting stage;
[0018] ③ After the self-cooling stage (300 seconds) and the air-cooling stage (240 seconds), number the samples and invert the crucible to remove the samples.
Embodiment 2
[0020] ①Put 6g of anhydrous lithium tetraborate lithium metaborate mixed flux, 0.5g of cobalt powder, 0.5g of sample and 0.3g of lithium nitrate into a yellow platinum crucible, then add 1ml of lithium bromide solution with a mass concentration of 27%;
[0021] ②After the first heat stage (time 180 seconds, temperature 600°C), second heat stage (time 180 seconds, temperature 1100°C), enter the melting stage (time 240 seconds, temperature 1100°C, swing speed 6 times / second), add 0.020g of potassium iodide during the 180-200 seconds of the melting stage;
[0022] ③ After the self-cooling stage (300 seconds) and the air-cooling stage (240 seconds), number the samples and invert the crucible to remove the samples.
Embodiment 3
[0024] ①Put 6g of anhydrous lithium tetraborate lithium metaborate mixed flux, 0.5g of cobalt powder, 0.5g of sample and 0.3g of lithium nitrate into a yellow platinum crucible, then add 1ml of lithium bromide solution with a mass concentration of 27%;
[0025] ②After the first heat stage (time 180 seconds, temperature 600°C), second heat stage (time 180 seconds, temperature 1100°C), enter the melting stage (time 240 seconds, temperature 1100°C, swing speed 6 times / second), add 0.025g potassium iodide during the period of 180 seconds to 200 seconds in the melting stage;
[0026] ③ After the self-cooling stage (300 seconds) and the air-cooling stage (240 seconds), number the samples and invert the crucible to remove the samples.
PUM
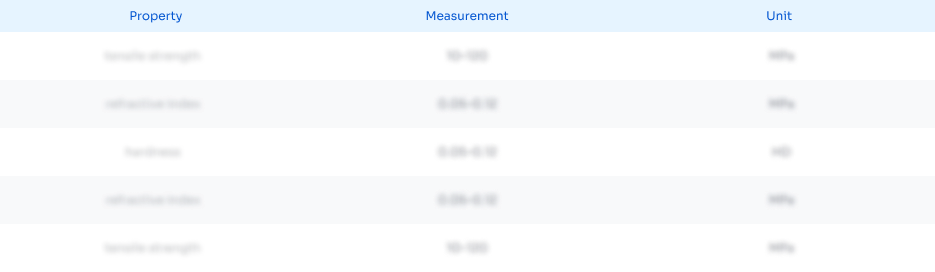
Abstract
Description
Claims
Application Information

- R&D
- Intellectual Property
- Life Sciences
- Materials
- Tech Scout
- Unparalleled Data Quality
- Higher Quality Content
- 60% Fewer Hallucinations
Browse by: Latest US Patents, China's latest patents, Technical Efficacy Thesaurus, Application Domain, Technology Topic, Popular Technical Reports.
© 2025 PatSnap. All rights reserved.Legal|Privacy policy|Modern Slavery Act Transparency Statement|Sitemap|About US| Contact US: help@patsnap.com