Composite purification packaging bag and preparation method thereof
A compound purification and packaging bag technology, applied in the field of purification packaging bags, can solve the problems of toughness, tear resistance, scratch resistance and poor flame retardancy, so as to improve tear resistance, good mechanical properties, and improve gloss Effects of Sex and Transparency
- Summary
- Abstract
- Description
- Claims
- Application Information
AI Technical Summary
Problems solved by technology
Method used
Image
Examples
Embodiment 1-4
[0029] Composite purification packaging bag is prepared according to the ratio in Table 1 (in parts by weight):
[0030]
Example 1
Example 2
Example 3
Example 4
HDPE
50
60
52
55
LLDPE
45
35
39
40
POE
10
10
10
10
10
10
10
10
[0031] Table 1
[0032] The preparation method of embodiment 1-4 comprises the following steps:
[0033] (1) Add ultrafine calcium carbonate into ultrapure water, ultrasonically disperse for 30 minutes, add zirconium isopropoxide, tetraethyl orthosilicate, water, ethanol, heat to 75°C, stir magnetically for 10 hours, centrifuge at 8000rpm for 20 Minutes later, the mixture was obtained, and the mixture was washed twice with deionized water, then placed in a muffle furnace, pyrolyzed at 450°C for 1 hour, cooled to room temperature, and ground to obtain composite calcium carbonate, wherein, ultrafine calcium carbonate, ultrapur...
PUM
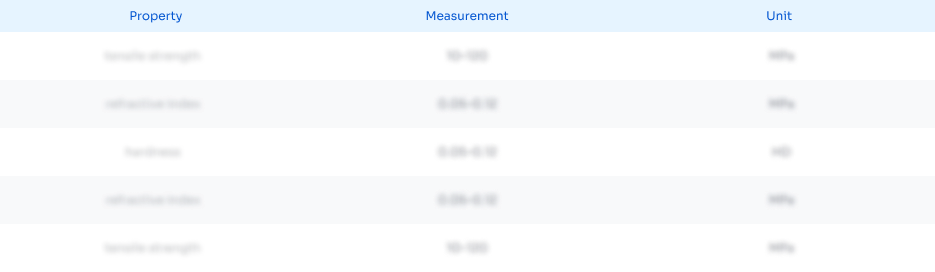
Abstract
Description
Claims
Application Information

- R&D
- Intellectual Property
- Life Sciences
- Materials
- Tech Scout
- Unparalleled Data Quality
- Higher Quality Content
- 60% Fewer Hallucinations
Browse by: Latest US Patents, China's latest patents, Technical Efficacy Thesaurus, Application Domain, Technology Topic, Popular Technical Reports.
© 2025 PatSnap. All rights reserved.Legal|Privacy policy|Modern Slavery Act Transparency Statement|Sitemap|About US| Contact US: help@patsnap.com