Antique looking green glaze
A green glaze and raw material technology, applied in the field of glaze, can solve the problems of low yield, poor jade texture, unnatural color development, etc., and achieve the effect of ensuring stability
- Summary
- Abstract
- Description
- Claims
- Application Information
AI Technical Summary
Problems solved by technology
Method used
Image
Examples
Embodiment 1
[0020] An antique green glaze prepared from the following raw materials in parts by weight: 9-15 parts of this medicine, 10-16 parts of quartz, 10-14 parts of calcite, 4-6 parts of limestone, 37-43 parts of feldspar, and 0.5 parts of tin block -1.5 parts, copper ore 2.5-3.5 parts, wood ash 7-13 parts, bone ash 3.5-4.5 parts.
[0021] The preparation method of above-mentioned antique green glaze, comprises the following steps:
[0022] (1) Preparation of glaze slurry: Add appropriate amount of water to mix the above raw materials, and ball mill to obtain glaze slurry with a mass concentration of 55-57%;
[0023] (2) Glazing: immerse the green body in the glaze slurry prepared in step (1) for a while, then immerse it again for a while, take it out, and use the water absorption of the green body to make the glaze slurry evenly adhere to the surface of the green body;
[0024] (3) Firing, the firing temperature is 1260-1280°C;
[0025] The firing process specifically includes th...
Embodiment 2
[0032] An antique green glaze prepared from the following raw materials in parts by weight: 12 parts of this medicine, 13 parts of quartz, 12 parts of calcite, 5 parts of limestone, 40 parts of feldspar, 1 part of tin block, 3 parts of copper ore, and 10 parts of wood ash 4 copies of ashes.
[0033] The preparation method of above-mentioned antique green glaze, comprises the following steps:
[0034] (1) Preparation of glaze slurry: Add appropriate amount of water to mix the above raw materials, and ball mill to obtain glaze slurry with a mass concentration of 56%;
[0035] (2) Glazing: immerse the green body in the glaze slurry prepared in step (1) for a while, then immerse it again for a while, take it out, and use the water absorption of the green body to make the glaze slurry evenly adhere to the surface of the green body;
[0036] (3) Firing, the firing temperature is 1270°C;
[0037] The firing process specifically includes the following steps:
[0038] ① Oxidation fl...
Embodiment 3
[0044] An antique green glaze prepared from the following raw materials in parts by weight: 10 parts of this medicine, 12 parts of quartz, 14 parts of calcite, 6 parts of limestone, 43 parts of feldspar, 0.7 part of tin block, 3.5 parts of copper ore, and 12 parts of wood ash parts, 4.5 parts of ashes.
[0045] The preparation method of above-mentioned antique green glaze, comprises the following steps:
[0046] (1) Preparation of glaze slurry: Add appropriate amount of water to mix the above raw materials, and ball mill to obtain glaze slurry with a mass concentration of 55%;
[0047] (2) Glazing: immerse the green body in the glaze slurry prepared in step (1) for a while, then immerse it again for a while, take it out, and use the water absorption of the green body to make the glaze slurry evenly adhere to the surface of the green body;
[0048] (3) Firing, the firing temperature is 1260°C;
[0049] The firing process specifically includes the following steps:
[0050] ① ...
PUM
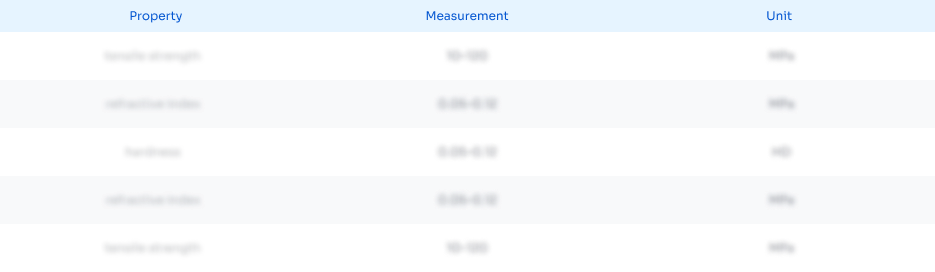
Abstract
Description
Claims
Application Information

- R&D Engineer
- R&D Manager
- IP Professional
- Industry Leading Data Capabilities
- Powerful AI technology
- Patent DNA Extraction
Browse by: Latest US Patents, China's latest patents, Technical Efficacy Thesaurus, Application Domain, Technology Topic, Popular Technical Reports.
© 2024 PatSnap. All rights reserved.Legal|Privacy policy|Modern Slavery Act Transparency Statement|Sitemap|About US| Contact US: help@patsnap.com