Covering yarn production device and method
The technology of a production device and production method, which is applied in the field of textile manufacturing and processing, can solve the problems affecting the quality of the core-spun yarn and unfavorable filament coating, etc., and achieve the effects of good evenness, high strength and improved yarn quality
- Summary
- Abstract
- Description
- Claims
- Application Information
AI Technical Summary
Problems solved by technology
Method used
Image
Examples
Embodiment 1
[0037] see Figure 1~4 , a core-spun yarn production device provided in an embodiment of the present invention, which sequentially includes a bell mouth 1, a first roller 2, a second roller 3, a third roller 4, a negative pressure tube 5 and a steel ring 6 from top to bottom, It is characterized in that a groove 7 is provided on the negative pressure tube 5, the groove 7 includes a first port 8 and a second port 9, the first port 8 is arranged above the second port 9, the The width of the first port 8 is greater than the width of the second port 9 .
[0038] The specific working process of this application: lead out the strands from the roving processed by the pre-spinning processes, feed the strands into the bell mouth 1 after passing through the yarn guide rod, and enter the drafting system after passing through the bell mouth 1, the first The top roller after the first roller 2 rotates to hold the strands and feeds them into the gripping area formed by the second roller 3 ...
Embodiment 2
[0040] see Figure 1~4 , a core-spun yarn production device provided in an embodiment of the present invention, which sequentially includes a bell mouth 1, a first roller 2, a second roller 3, a third roller 4, a negative pressure tube 5 and a steel ring 6 from top to bottom, It is characterized in that a groove 7 is provided on the negative pressure tube 5, the groove 7 includes a first port 8 and a second port 9, the first port 8 is arranged above the second port 9, the The width of the first port 8 is greater than the width of the second port 9 .
[0041] Optionally, the groove 7 includes a wedge-shaped groove, and the wedge-shaped groove is perpendicular to the negative pressure tube 5 .
[0042] Optionally, the groove 7 is in a "Y" shape, the first port 8 is 4.5 mm wide, and the second port 9 is 2.7 mm wide.
[0043] Optionally, a grid ring 10 is arranged on the groove 7 .
[0044]The specific working process of this application: lead out the strands from the roving pr...
Embodiment 3
[0047] see Figure 1~4 , a core-spun yarn production device provided in an embodiment of the present invention, which sequentially includes a bell mouth 1, a first roller 2, a second roller 3, a third roller 4, a negative pressure tube 5 and a steel ring 6 from top to bottom, It is characterized in that a groove 7 is provided on the negative pressure tube 5, the groove 7 includes a first port 8 and a second port 9, the first port 8 is arranged above the second port 9, the The width of the first port 8 is greater than the width of the second port 9 .
[0048] Optionally, the groove 7 is radial, and the groove 7 includes several first ports 8 .
[0049] Optionally, the groove 7 includes three first ports 8, and the width of the first ports 8 is 1mm.
[0050] Optionally, a grid ring 10 is arranged on the groove 7 .
[0051] The specific working process of this application: lead out the strands from the roving processed by the pre-spinning processes, feed the strands into the b...
PUM
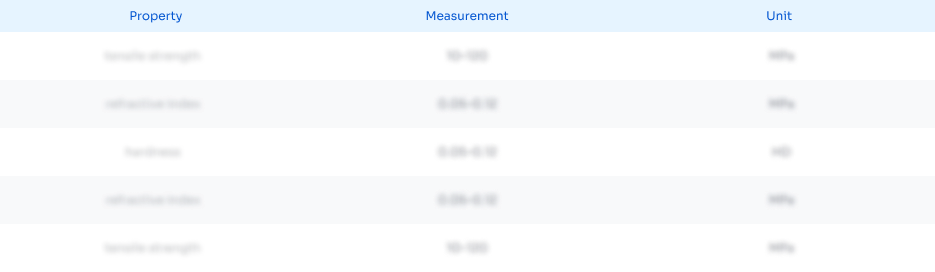
Abstract
Description
Claims
Application Information

- Generate Ideas
- Intellectual Property
- Life Sciences
- Materials
- Tech Scout
- Unparalleled Data Quality
- Higher Quality Content
- 60% Fewer Hallucinations
Browse by: Latest US Patents, China's latest patents, Technical Efficacy Thesaurus, Application Domain, Technology Topic, Popular Technical Reports.
© 2025 PatSnap. All rights reserved.Legal|Privacy policy|Modern Slavery Act Transparency Statement|Sitemap|About US| Contact US: help@patsnap.com