Refining process of polyoxypropylene ether
A technology of polyoxypropylene ether and process, which is applied in the field of polyoxypropylene ether refining technology, can solve the problems of inability to prepare high-purity polyoxypropylene ether, and achieve the effect of promoting development and improving purity
- Summary
- Abstract
- Description
- Claims
- Application Information
AI Technical Summary
Problems solved by technology
Method used
Image
Examples
Embodiment 1
[0039] In Example 1, crude polyoxypropylene ether was obtained by using hydroxypropyl methacrylate and propylene oxide with boron trifluoride as a catalyst.
[0040] Add 1000 parts of crude polyoxypropylene ether (including 5 parts of boron trifluoride) and 250 parts of water into a four-necked flask according to the mass ratio, stir evenly, raise the temperature to 75°C, add 10 parts of sodium hydroxide to neutralize and stir for 5-10 Minutes, adjust the pH to between 6-8, then add 3 parts of adsorbent as a pH buffer to absorb slightly excess acid or alkali, and stir for 5-10 minutes.
[0041] The salt obtained after neutralization is sodium fluoride and sodium borate, because sodium borate is more soluble in water at 60-80°C, while the solubility of sodium fluoride at 60-80°C is only about 4.5. Therefore, we add seeds when sodium fluoride is in a supersaturated state. It is calculated that the solution contains 9.3 parts of sodium fluoride, and it needs 207 parts of water t...
Embodiment 2
[0044] In Example 2, crude polyoxypropylene ether was obtained by using hydroxypropyl methacrylate and propylene oxide with boron trifluoride as a catalyst.
[0045] Add 1000 parts of crude polyoxypropylene ether (including 5 parts of boron trifluoride) and 250 parts of water into a four-necked flask according to the mass ratio, stir evenly, raise the temperature to 75°C, add 10 parts of sodium hydroxide to neutralize and stir for 5-10 Minutes, adjust the pH to between 6-8, then add 3 parts of adsorbent as a pH buffer to absorb slightly excess acid or alkali, and stir for 5-10 minutes.
[0046] After decompression and vacuum dehydration, adjust the vacuum to 300-250mbar, add 0.2 parts of NaH when the effluent is measured to 30 parts 2 P0 4 ·6H 2 0 as the seed crystal. Continue dehydration and keep the vacuum at 300-250mbar for 2 hours, 250-200mbar for 1 hour, 200-0mbar for 1 hour, raise the temperature to 85°C and keep 0mbar for 1 hour. Then stop dehydration and add 3 part...
Embodiment 3
[0048] In Example 3, crude polyoxypropylene ether was obtained by using hydroxypropyl methacrylate and propylene oxide with boron trifluoride as a catalyst.
[0049] Add 1000 parts of crude polyoxypropylene ether (including 5 parts of boron trifluoride) and 250 parts of water into a four-necked flask according to the mass ratio, stir evenly, raise the temperature to 75°C, add 10 parts of sodium hydroxide to neutralize and stir for 5-10 Minutes, adjust the pH to between 6-8, then add 3 parts of adsorbent as a pH buffer to absorb slightly excess acid or alkali, and stir for 5-10 minutes.
[0050] After decompression and vacuum dehydration, adjust the vacuum to 300-250mbar, add 0.2 parts of NaH when the effluent is measured to 40 parts 2 P0 4 ·6H 2 0 as the seed crystal. Continue dehydration and keep the vacuum at 300-250mbar for 2 hours, 250-200mbar for 1 hour, 200-0mbar for 1 hour, raise the temperature to 85°C and keep 0mbar for 1 hour. Then stop dehydration and add 3 part...
PUM
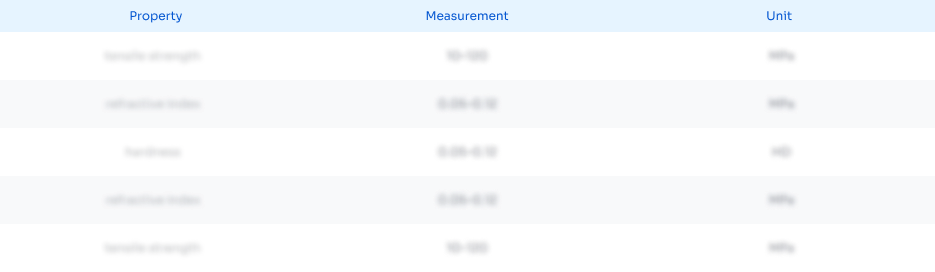
Abstract
Description
Claims
Application Information

- Generate Ideas
- Intellectual Property
- Life Sciences
- Materials
- Tech Scout
- Unparalleled Data Quality
- Higher Quality Content
- 60% Fewer Hallucinations
Browse by: Latest US Patents, China's latest patents, Technical Efficacy Thesaurus, Application Domain, Technology Topic, Popular Technical Reports.
© 2025 PatSnap. All rights reserved.Legal|Privacy policy|Modern Slavery Act Transparency Statement|Sitemap|About US| Contact US: help@patsnap.com