Hot primary air heating system for dry coal pulverizing system
A pulverizing system and heating system technology, applied in the field of boilers, can solve the problems of reducing the secondary air rate, affecting the rigidity of the secondary air, and increasing the power consumption of the primary fan, so as to reduce the operating cost and improve the drying output.
- Summary
- Abstract
- Description
- Claims
- Application Information
AI Technical Summary
Problems solved by technology
Method used
Image
Examples
Embodiment Construction
[0013] Below in conjunction with specific embodiment, further illustrate the present invention. It should be understood that these examples are only used to illustrate the present invention and are not intended to limit the scope of the present invention. In addition, it should be understood that after reading the teachings of the present invention, those skilled in the art can make various changes or modifications to the present invention, and these equivalent forms also fall within the scope defined by the appended claims of the present application.
[0014] In order to solve the problems pointed out in the background technology, the present invention proposes to add a heat exchanger in the hot primary air duct in front of the coal mill to reheat the hot primary air twice, and after the air duct is reformed, the hot primary air rate returns to the original Design parameters to ensure the drying capacity of the coal mill, and at the same time, the side outlet temperature of t...
PUM
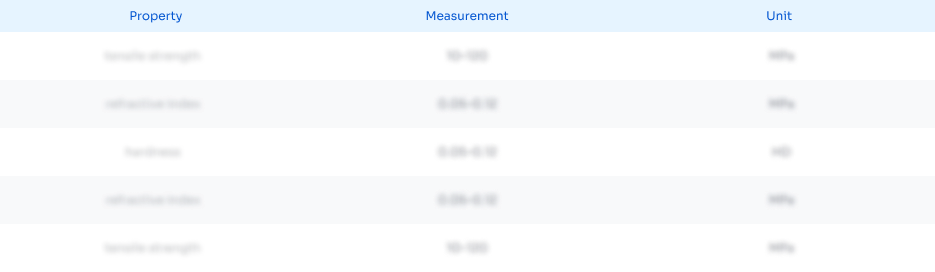
Abstract
Description
Claims
Application Information

- R&D Engineer
- R&D Manager
- IP Professional
- Industry Leading Data Capabilities
- Powerful AI technology
- Patent DNA Extraction
Browse by: Latest US Patents, China's latest patents, Technical Efficacy Thesaurus, Application Domain, Technology Topic, Popular Technical Reports.
© 2024 PatSnap. All rights reserved.Legal|Privacy policy|Modern Slavery Act Transparency Statement|Sitemap|About US| Contact US: help@patsnap.com