Method for recycling iron resource from soft manganese ore leaching slag
A technology for leaching slag and pyrolusite, which is applied in the field of recycling iron-containing waste slag, can solve the problems of waste of iron resources and secondary pollution of the environment, and achieve the effects of avoiding waste, low cost, and reducing secondary pollution
- Summary
- Abstract
- Description
- Claims
- Application Information
AI Technical Summary
Problems solved by technology
Method used
Image
Examples
Embodiment 1
[0031] A method for recovering iron resources from pyrolusite leaching slag, the operation steps are as follows:
[0032] (1) Leaching: use oxalic acid solution with oxalic acid concentration of 1.5mol / L as leaching agent, after measuring the iron content in pyrolusite, mix oxalic acid solution with pyrolus slag according to the molar ratio of oxalic acid and iron as 3:1 Slurry, leaching for 4.5 hours at a temperature of 95°C and a stirring speed of 250r / min, so that the iron in the soft manganese slag is converted into soluble iron oxalate;
[0033] (2) Solid-liquid separation: centrifuging the leached slurry in step (1) to obtain waste residue and leachate containing ferric oxalate;
[0034] (3) Immerse iron in phosphate: add phosphoric acid to the leachate obtained in step (2), the molar ratio of the amount of phosphoric acid added to the iron in the leachate is 0.9:1, stirring and reacting for 1h under the condition that the rotating speed is 100r / min makes the oxalic acid...
Embodiment 2
[0038] A method for recovering iron resources from pyrolusite leaching slag, the operation steps are as follows:
[0039] (1) Leaching: Use a mixed solution with an oxalic acid concentration of 1.5mol / L and an ammonium oxalate concentration of 0.5mol / L as a leaching agent. After measuring the iron content in pyrolusite, the molar ratio of oxalate to iron is 2:1 , wherein the molar ratio of oxalic acid to iron is 1.5:1, the mixed solution is mixed with soft manganese slag to make pulp, and stirred and leached for 6 hours at a temperature of 90°C and a stirring speed of 300r / min, so that the iron in the soft manganese slag into soluble ferric oxalate;
[0040] (2) Solid-liquid separation: press-filter the slurry after leaching in step (1) to obtain waste residue and leachate containing ferric oxalate;
[0041](3) Phosphate heavy iron: add phosphoric acid in step (2) gained leaching solution, the mol ratio of the addition of phosphoric acid and iron in leaching solution is 0.95:...
PUM
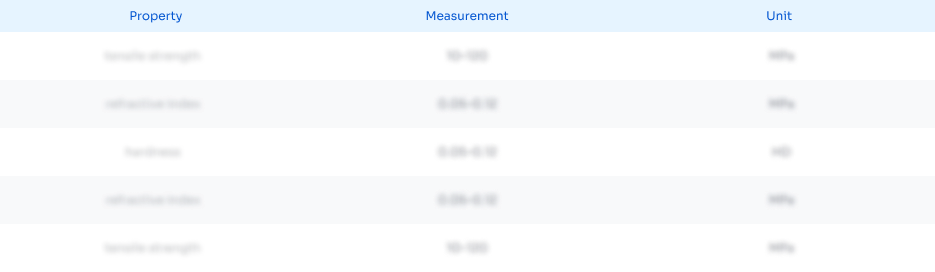
Abstract
Description
Claims
Application Information

- Generate Ideas
- Intellectual Property
- Life Sciences
- Materials
- Tech Scout
- Unparalleled Data Quality
- Higher Quality Content
- 60% Fewer Hallucinations
Browse by: Latest US Patents, China's latest patents, Technical Efficacy Thesaurus, Application Domain, Technology Topic, Popular Technical Reports.
© 2025 PatSnap. All rights reserved.Legal|Privacy policy|Modern Slavery Act Transparency Statement|Sitemap|About US| Contact US: help@patsnap.com