Layered potassium calcium phosphate compounding lithium-base lubricating grease composition and preparation method of same
A technology based on lubricating grease and potassium calcium phosphate, which is applied in the direction of lubricating compositions, phosphorus compounds, chemical instruments and methods, etc., can solve the problems of impurity symbiosis, etc., and achieve the effects of mild conditions, abundant raw material sources, and simple synthesis methods
- Summary
- Abstract
- Description
- Claims
- Application Information
AI Technical Summary
Problems solved by technology
Method used
Image
Examples
Embodiment 1
[0029] Add raw materials into a 30 mL polytetrafluoroethylene stainless steel kettle: 1.11 g calcium chloride, 1.74 g dipotassium hydrogen phosphate, and react in 10 mL aqueous solution. Temperature 100 ℃, react for 3 days, filter, wash with distilled water, and dry at room temperature to obtain layered potassium calcium phosphate CaKPO 4 ·H 2 O. figure 1 Be the XRD figure of this product.
[0030] Add 28.0 g of PAO9 and 9.0 g of 12-hydroxystearic acid into the fat-making kettle, heat up and melt, and slowly add lithium hydroxide aqueous solution (containing 1.5 g of lithium hydroxide) at a temperature of 105 °C. After the lithium hydroxide solution was added, the temperature rose rapidly to 170 °C to completely dehydrate the soap base, and the material was quickly cooled to 105 °C, 4.0 g of azelaic acid was added, stirred for 10 min, and lithium hydroxide aqueous solution (containing Lithium 1.5 g) to saponify azelaic acid, the temperature was raised to 170 °C and kept for...
Embodiment 2
[0035] Add 0.40 g of calcium acetate, 1.86 g of potassium chloride and 2.45 g of phosphoric acid into a 30 mL polytetrafluoroethylene stainless steel kettle, and react in 22.5 mL of water. Temperature 150 ℃, react for 2 days, filter, wash with distilled water, and dry at room temperature to obtain layered potassium calcium phosphate CaKPO 4 ·H 2 O.
[0036]Add 31.3 g of 100 SN and 4.0 g of stearic acid to the fat-making kettle, heat up and melt, and slowly add lithium hydroxide aqueous solution (containing 0.5 g of lithium hydroxide) at a temperature of 80 °C. After the lithium hydroxide solution was added, the temperature rose rapidly to 130 °C to completely dehydrate the soap base, and the material was rapidly cooled to 90 °C, and 1.0 g of adipic acid was added, stirred for 10 min, and then lithium hydroxide aqueous solution (containing Lithium 0.5 g) to saponify adipic acid, the temperature was raised to 130 °C and kept for 1 h to complete the dehydration, the temperature...
Embodiment 3
[0041] Add raw materials into a 30 mL polytetrafluoroethylene stainless steel kettle: 2.72 g calcium sulfate, 8.16 g potassium dihydrogen phosphate and 5.88 g potassium acetate, and react in 18 mL water. Temperature 25 ℃, react for 7 days, filter, wash with distilled water, and dry at room temperature to obtain layered potassium calcium phosphate CaKPO 4 ·H 2 O.
[0042] Add 29.0 g of liquid paraffin and 8.0 g of stearic acid to the fat-making kettle, heat up and melt, and slowly add lithium hydroxide aqueous solution (containing 1.0 g of lithium hydroxide) at a temperature of 100 °C. After the lithium hydroxide solution was added, the temperature rose rapidly to 150 °C to completely dehydrate the soap base. The material was quickly cooled to 100 °C, 3.0 g of adipic acid was added, stirred for 10 min, and lithium hydroxide aqueous solution (containing hydroxide Lithium 1.0 g) to saponify adipic acid, raise the temperature to 150°C and keep for 1 h to complete the dehydration...
PUM
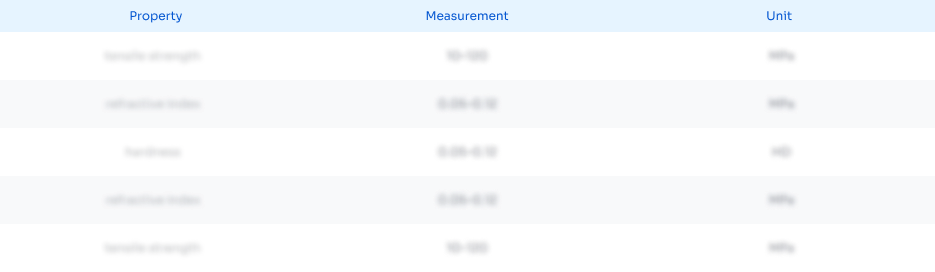
Abstract
Description
Claims
Application Information

- R&D Engineer
- R&D Manager
- IP Professional
- Industry Leading Data Capabilities
- Powerful AI technology
- Patent DNA Extraction
Browse by: Latest US Patents, China's latest patents, Technical Efficacy Thesaurus, Application Domain, Technology Topic, Popular Technical Reports.
© 2024 PatSnap. All rights reserved.Legal|Privacy policy|Modern Slavery Act Transparency Statement|Sitemap|About US| Contact US: help@patsnap.com