Preparation method for graphene/copper composite powder material
A composite powder and graphene technology, applied in graphene, nano-carbon and other directions, can solve the problems of high cost, prone to agglomeration, uneven composition, etc., and achieve the effect of mass production, uniform dispersion and stable structure
- Summary
- Abstract
- Description
- Claims
- Application Information
AI Technical Summary
Problems solved by technology
Method used
Image
Examples
Embodiment 1
[0023] Get 1800mL concentration and be that the graphene oxide (carbon content is 65%) aqueous solution that is 1.2mg / mL, and stir with rotating speed 1500rpm in high-speed shear mixer, then add 120 grams of copper acetate monohydrate (copper The content is 38.2g). After the mixing is completed, continue to carry out high-speed shear stirring at the same speed, and use a spray dryer (small spray dryer H-Spray Mini, Beijing Halls Biotechnology Co., Ltd.) to dry the mixed solution at the same time, and the extraction volume is 6mL / min. The wind temperature is 220°C, and the air outlet temperature is 120°C (drying gas flow rate is 800L / h, the same as in the following examples). In the spray drying process, the high-speed shear stirring can be taken in an intermittent manner, and the shear speed is 1500rpm. Among them, the high-speed shear When cutting and stirring, keep the temperature of the solution at 30-35°C. When the solution temperature reaches 35°C, stop shearing and stirr...
Embodiment 2
[0025] Take 1800mL of graphene oxide aqueous solution whose concentration is 0.12mg / mL, wherein the carbon content in graphene oxide is 65%, and stir in a high-speed shear mixer at a speed of 2000rpm, and then add 120 grams of acetic acid monohydrate during the stirring process Copper, wherein the copper content is 38.2g. After the mixing is completed, use a spray dryer (small spray dryer H-Spray Mini, Beijing Halls Biotechnology Co., Ltd.) to dry the mixed solution. ℃, the high-speed shear stirring is intermittently used during the spray drying process, and the shear speed is 2000rpm to ensure that the mixed solution does not exceed 35°C during the whole process. Shear stirring at the same speed was resumed again. After spray drying, the precursor powder was obtained, and the temperature was raised in a hydrogen atmosphere at a rate of 200°C / min. After reaching 350°C, the temperature was kept for 30 minutes, and the mixed powder was reduced. A graphene / copper composite powd...
Embodiment 3
[0027] Take 1800mL of graphene oxide aqueous solution with a concentration of 0.04mg / mL, wherein the carbon content in graphene oxide is 65%, and stir in a high-speed shear mixer at a speed of 2000rpm, and then slowly add 120 grams of monowater during the stirring process Copper acetate, wherein the copper content is 38.2g. After the mixing is completed, use a spray dryer (small spray dryer H-Spray Mini, Beijing Halls Biotechnology Co., Ltd.) to dry the mixed solution. ℃, the high-speed shear stirring is intermittently used during the spray drying process, and the shear speed is 1500rpm to ensure that the mixed solution does not exceed 35°C during the whole process. Resume shear stirring at the same speed. After spray drying, the precursor powder was obtained, and the temperature was raised in a hydrogen atmosphere at a rate of 10°C / min. After reaching 350°C, the temperature was kept for 30 minutes, and the mixed powder was reduced. A graphene / copper composite powder with a ...
PUM
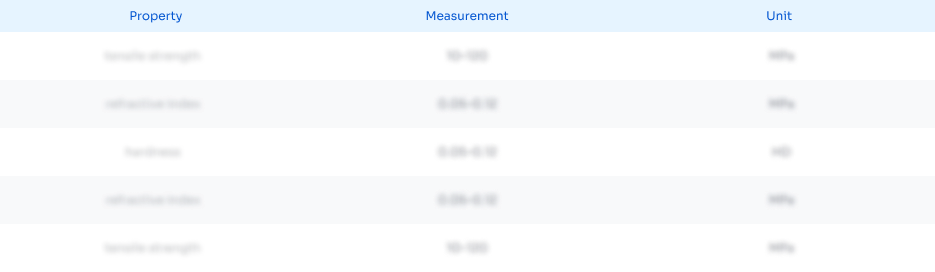
Abstract
Description
Claims
Application Information

- R&D Engineer
- R&D Manager
- IP Professional
- Industry Leading Data Capabilities
- Powerful AI technology
- Patent DNA Extraction
Browse by: Latest US Patents, China's latest patents, Technical Efficacy Thesaurus, Application Domain, Technology Topic, Popular Technical Reports.
© 2024 PatSnap. All rights reserved.Legal|Privacy policy|Modern Slavery Act Transparency Statement|Sitemap|About US| Contact US: help@patsnap.com