Gap-adjustable automatic calendering device for graphite heat-dissipation film
A graphite heat dissipation film and calendering device technology, which is applied in the lamination device, lamination, lamination auxiliary operations, etc., can solve the problem of insufficient smoothness and cleanliness of the surface of the pressing roller, increase the falling particles of the graphite heat dissipation film, and the rough surface of the graphite heat dissipation film To achieve the effect of saving raw materials, improving production flexibility, and smooth and clean surface
- Summary
- Abstract
- Description
- Claims
- Application Information
AI Technical Summary
Problems solved by technology
Method used
Image
Examples
Embodiment Construction
[0021] Such as Figure 1-Figure 3 As shown, a graphite heat dissipation film automatic calendering device with adjustable gap includes an upper pressure roller 1 and a lower pressure roller 2 for calendering graphite heat dissipation film, PET release film and auxiliary film, and also includes a The first unwinding roller 3 of the unwinding graphite heat dissipation film at the front end, the second unwinding roller 4 of unwinding the PET release film, the third unwinding roller 5 of the unwinding auxiliary film, and the take-up roller arranged at the rear end of its conveying material The first winding roller 6 for rolling the finished graphite heat dissipation film after rolling, and the second winding roller 7 for winding the auxiliary film.
[0022] An automatic calendering device for a graphite cooling film with an adjustable gap in this embodiment, by adding an auxiliary film as an adaptation layer when rolling the graphite cooling film and the PET release film, the auxi...
PUM
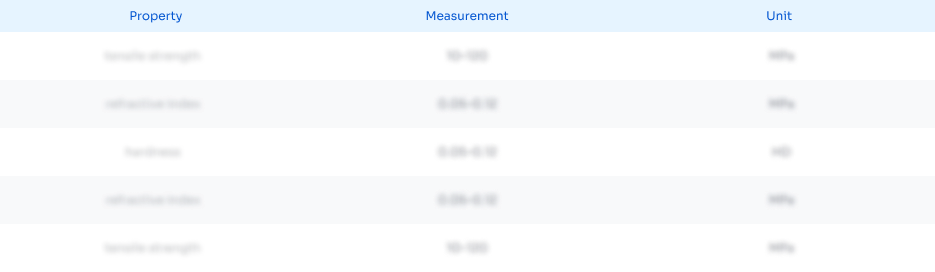
Abstract
Description
Claims
Application Information

- R&D
- Intellectual Property
- Life Sciences
- Materials
- Tech Scout
- Unparalleled Data Quality
- Higher Quality Content
- 60% Fewer Hallucinations
Browse by: Latest US Patents, China's latest patents, Technical Efficacy Thesaurus, Application Domain, Technology Topic, Popular Technical Reports.
© 2025 PatSnap. All rights reserved.Legal|Privacy policy|Modern Slavery Act Transparency Statement|Sitemap|About US| Contact US: help@patsnap.com