A method for shaping and implanting an optical fiber sensing network into a projectile structure
A technology of sensing network and optical fiber, applied in ammunition testing, ammunition, offensive equipment, etc., can solve problems such as complicated metal slotting process, surface damage of structure, and limited application range, so as to improve system security and reliability , high heat insulation and flame retardant properties, good environmental adaptability
- Summary
- Abstract
- Description
- Claims
- Application Information
AI Technical Summary
Problems solved by technology
Method used
Image
Examples
Embodiment Construction
[0025] The method of the present invention will be further described in conjunction with the accompanying drawings.
[0026] Such as figure 1 Shown, a kind of optical fiber sensory network shape-implanting method for projectile structure, comprises the following steps:
[0027] Step 1: Paste the rectangular cork board on the surface of the metal casing 1 of the missile, cut and splice it so that the cork completely covers the surface of the metal casing 1 to form a cork layer 2, and then cut off the cork layer 2 with a specific path according to the design drawing to form a structure that can accommodate the missile. The optical fiber groove 3 where the optical fiber 4 is laid.
[0028] Step 2: Lay the sensing optical fiber 4 into the fiber groove 3 one by one, the specific operation is as follows, paste double-sided tape in each fiber groove 3, the double-sided tape has a width of 2 mm and a length of 10 mm, and every 10 cm Paste a double-sided adhesive tape, lay the sensin...
PUM
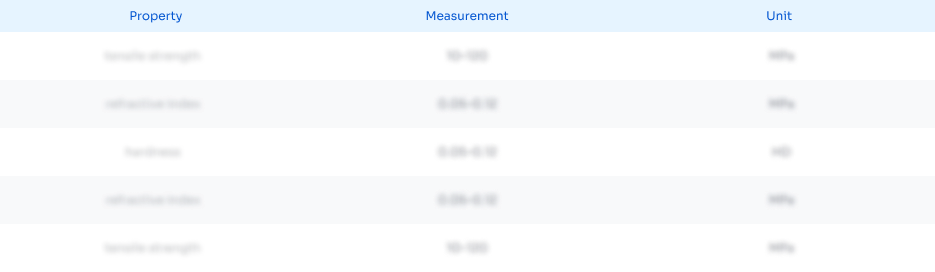
Abstract
Description
Claims
Application Information

- Generate Ideas
- Intellectual Property
- Life Sciences
- Materials
- Tech Scout
- Unparalleled Data Quality
- Higher Quality Content
- 60% Fewer Hallucinations
Browse by: Latest US Patents, China's latest patents, Technical Efficacy Thesaurus, Application Domain, Technology Topic, Popular Technical Reports.
© 2025 PatSnap. All rights reserved.Legal|Privacy policy|Modern Slavery Act Transparency Statement|Sitemap|About US| Contact US: help@patsnap.com