High-elasticity flame-retarding wood-plastic packaging material and preparation method thereof
A packaging material and high-elasticity technology, applied in the field of wood-plastic packaging materials, can solve the problems of easily damaged products, products and packaging materials that are prone to fire, and poor flame-retardant effect, and achieve the effect of improving elasticity and flame retardancy
- Summary
- Abstract
- Description
- Claims
- Application Information
AI Technical Summary
Problems solved by technology
Method used
Examples
Embodiment 1
[0021] S1: 50 parts of plant fiber and 8 parts of carbon fiber were crushed into powder, 10 parts of 10% sodium bicarbonate aqueous solution was added to it, and stirred at a temperature of 40 ° C for 1 h; Stir and react at ℃ for 0.5h; after filtering, add 7 parts of titanate coupling agent, stir and react at a temperature of 100°C for 3h, and obtain a fiber mixture after filtering;
[0022] S2: Mix the fiber mixture described in step S1, 1 part of aluminum silicate, 15 parts of polyvinyl chloride, 15 parts of polypropylene, 6 parts of polybutylene succinate, and 7 parts of tributyl phosphate into the mixer , stirring and reacting at a temperature of 100°C and a rate of 1500r / min for 20min;
[0023] S3: Add the mixture obtained in step S2 into an extruder, the extrusion temperature is 180°C, and the screw speed is 40rpm;
[0024] S4: Put the extruded material obtained in step S3 into a granulator to granulate; add 3 parts of cerium phosphate, 15 parts of linalool and 8 parts ...
Embodiment 2
[0027] S1: 70 parts of plant fiber and 10 parts of carbon fiber were pulverized into powder, and 15 parts of 10% sodium bicarbonate aqueous solution was added to it, and stirred at a temperature of 60°C for 3 hours; Stir and react at ℃ for 3 hours; after filtering, add 3 parts of titanate coupling agent, stir and react at a temperature of 80℃ for 2 hours, and obtain a fiber mixture after filtering;
[0028] S2: Mix the fiber mixture described in step S1, 3 parts of aluminum silicate, 10 parts of polyvinyl chloride, 20 parts of polypropylene, 10 parts of polybutylene succinate, and 9 parts of tributyl phosphate into the mixer , stirring and reacting at a temperature of 118°C and a rate of 1800r / min for 40min;
[0029] S3: Add the mixture obtained in step S2 into an extruder, the extrusion temperature is 210° C., and the screw speed is 60 rpm;
[0030] S4: Put the extruded material obtained in step S3 into a granulator to granulate; add 6 parts of cerium phosphate, 20 parts of ...
Embodiment 3
[0033] S1: 55 parts of plant fiber and 9 parts of carbon fiber were pulverized into powder, 12 parts of 10% sodium bicarbonate aqueous solution was added to it, and stirred at a temperature of 45°C for 1.5 h; Stir and react at 65°C for 1 hour; after filtering, add 6 parts of titanate coupling agent, stir and react at 88°C for 2 hours, and obtain a fiber mixture after filtration;
[0034] S2: Mix the fiber mixture described in step S1, 1 part of aluminum silicate, 13 parts of polyvinyl chloride, 18 parts of polypropylene, 8 parts of polybutylene succinate, and 9 parts of tributyl phosphate into the mixer , stirring and reacting at a temperature of 105°C and a rate of 1600r / min for 25min;
[0035] S3: Add the mixture obtained in step S2 into an extruder, the extrusion temperature is 200° C., and the screw speed is 45 rpm;
[0036] S4: Put the extruded material obtained in step S3 into a granulator to granulate; add 4 parts of cerium phosphate, 17 parts of linalool and 10 parts ...
PUM
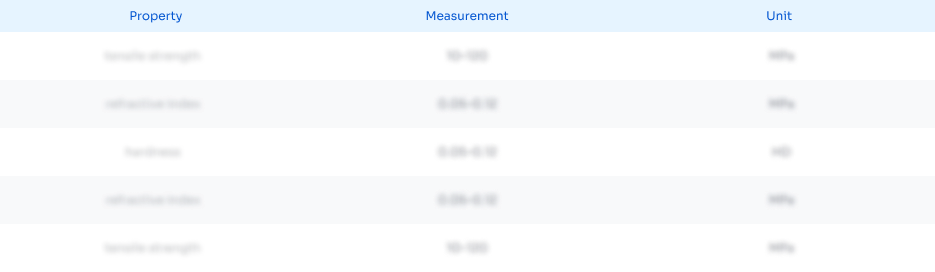
Abstract
Description
Claims
Application Information

- Generate Ideas
- Intellectual Property
- Life Sciences
- Materials
- Tech Scout
- Unparalleled Data Quality
- Higher Quality Content
- 60% Fewer Hallucinations
Browse by: Latest US Patents, China's latest patents, Technical Efficacy Thesaurus, Application Domain, Technology Topic, Popular Technical Reports.
© 2025 PatSnap. All rights reserved.Legal|Privacy policy|Modern Slavery Act Transparency Statement|Sitemap|About US| Contact US: help@patsnap.com