Preparation method of circuit board water-based cleaning agent
A cleaning agent, board water-based technology, applied in the field of cleaning agents, can solve the problems of poor cleaning performance compared with chlorofluorocarbons, strong damage to personnel health, low flash point and explosiveness, etc., and achieves low cost, good safety and reasonable formula Effect
- Summary
- Abstract
- Description
- Claims
- Application Information
AI Technical Summary
Problems solved by technology
Method used
Examples
Embodiment 1
[0016] A method for preparing a water-based cleaning agent for circuit boards, comprising the following steps: (1) Weighing the following components by weight: 10 parts of benzotriazole, 18 parts of butyl acetate, 1.2 parts of ethanolamine, and 3 parts of isopropanol , 0.5 parts of nitroethane, 0.5 parts of sodium lauryl alcohol polyoxyethylene ether carboxylate, 3 parts of nonylphenol polyoxyethylene ether, 2.5 parts of polyoxyethylene monostearate, 3 parts of D-limonene, 1.5 parts of potassium lauryl ether phosphate, 30 parts of ethanol, 1.2 parts of tetrasodium hydroxyethylidene diphosphonate, 40 parts of deionized water; (2) Add benzotriazole, nonylphenol polyoxyethylene to the reaction kettle Ether, D-limonene, butyl acetate, ethanolamine, sodium lauryl alcohol polyoxyethylene ether carboxylate, ethanol, mixed and stirred for 20 minutes; (3) continue to add isopropanol, polyoxyethylene monostearate, nitric acid ethyl ethane, potassium lauryl ether phosphate, and stir well...
Embodiment 2
[0018] A method for preparing a water-based cleaning agent for circuit boards, comprising the following steps: (1) Weighing the following components by weight: 6 parts of benzotriazole, 16 parts of butyl acetate, 2.5 parts of ethanolamine, and 4 parts of isopropanol , 1.2 parts of nitroethane, 1 part of sodium lauryl alcohol polyoxyethylene ether carboxylate, 5 parts of nonylphenol polyoxyethylene ether, 1.8 parts of polyoxyethylene monostearate, 1 part of D-limonene, 0.5 parts of potassium lauryl ether phosphate, 28 parts of ethanol, 1.5 parts of tetrasodium hydroxyethylidene diphosphonate, 45 parts of deionized water; (2) Add benzotriazole, nonylphenol polyoxyethylene to the reaction kettle Ether, D-limonene, butyl acetate, ethanolamine, sodium lauryl alcohol polyoxyethylene ether carboxylate, ethanol, mixed and stirred for 10 minutes; (3) continue to add isopropanol, polyoxyethylene monostearate, nitric acid ethyl ethane, potassium lauryl ether phosphate, and stir well for ...
Embodiment 3
[0020] A method for preparing a water-based cleaning agent for circuit boards, comprising the following steps: (1) Weighing the following components by weight: 8 parts of benzotriazole, 14 parts of butyl acetate, 1.5 parts of ethanolamine, and 3 parts of isopropanol , 0.8 parts of nitroethane, 1.5 parts of sodium lauryl alcohol polyoxyethylene ether carboxylate, 4 parts of nonylphenol polyoxyethylene ether, 2.2 parts of polyoxyethylene monostearate, 2 parts of D-limonene, 1.2 parts of potassium lauryl ether phosphate, 23 parts of ethanol, 1.5 parts of tetrasodium hydroxyethylidene diphosphonate and 55 parts of deionized water; (2) Add benzotriazole and nonylphenol polyoxyethylene ether into the reaction kettle , D-limonene, butyl acetate, ethanolamine, sodium lauryl alcohol polyoxyethylene ether carboxylate, ethanol, mixed and stirred for 15 minutes; (3) continue to add isopropanol, polyoxyethylene monostearate, nitro Ethane, potassium lauryl ether phosphate, and stir well for...
PUM
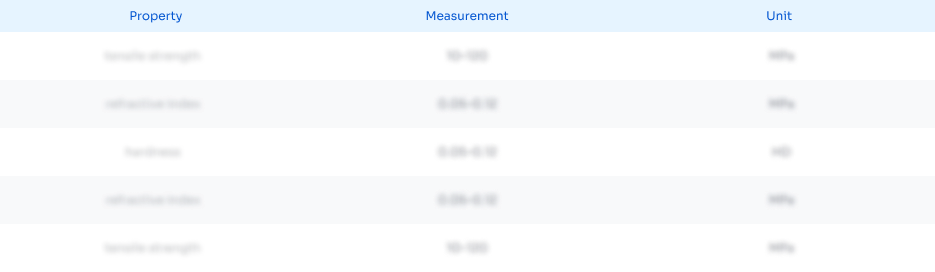
Abstract
Description
Claims
Application Information

- R&D
- Intellectual Property
- Life Sciences
- Materials
- Tech Scout
- Unparalleled Data Quality
- Higher Quality Content
- 60% Fewer Hallucinations
Browse by: Latest US Patents, China's latest patents, Technical Efficacy Thesaurus, Application Domain, Technology Topic, Popular Technical Reports.
© 2025 PatSnap. All rights reserved.Legal|Privacy policy|Modern Slavery Act Transparency Statement|Sitemap|About US| Contact US: help@patsnap.com