Powder coating
A powder coating and zinc powder technology, applied in powder coatings, polyester coatings, coatings, etc., can solve the problems of easy cracking and falling off, low hardness, affecting the use and appearance of powder coatings, and achieve low cost and high hardness. High, maintain the effect of protective performance and appearance effect
- Summary
- Abstract
- Description
- Claims
- Application Information
AI Technical Summary
Problems solved by technology
Method used
Examples
Embodiment 1
[0014] A powder coating, in parts by weight, its components are: 70 parts of magnesium carbonate, 4.5 parts of mica powder, 3.5 parts of cellulose, 4 parts of fluorescent powder, 4.5 parts of porcelain calcium, 7.5 parts of bentonite, 6 parts of rubber powder 70 parts of polyester resin, 22.5 parts of curing agent, 37.5 parts of zinc powder, 10 parts of antioxidant, 5 parts of benzoin, 3 parts of brightening agent.
[0015] Zinc powder is titanium dioxide.
[0016] A kind of processing method of powder coating, concrete method is as follows:
[0017] (1) All materials are weighed according to the proportion, after mixing;
[0018] (2) Extruded in a twin-screw extruder at about 120-135°C;
[0019] (3) The extruded tablet is crushed and passed through a 120-200 mesh sieve.
Embodiment 2
[0021] A powder coating, in parts by weight, its components are: 60 parts of magnesium carbonate, 4 parts of mica powder, 2 parts of cellulose, 3 parts of fluorescent powder, 4 parts of porcelain calcium, 5 parts of bentonite, 2 parts of rubber powder ; 60 parts of polyester resin, 20 parts of curing agent, 35 parts of zinc powder, 8-12 parts of antioxidant, 4 parts of benzoin, 2 parts of brightening agent.
[0022] A kind of processing method of powder coating, concrete method is as follows:
[0023] (1) All materials are weighed according to the proportion, after mixing;
[0024] (2) Extruded in a twin-screw extruder at about 120-135°C;
[0025] (3) The extruded tablet is crushed and passed through a 120-200 mesh sieve.
Embodiment 3
[0028] A powder coating, in parts by weight, its components are: 80 parts of magnesium carbonate, 5 parts of mica powder, 5 parts of cellulose, 5 parts of fluorescent powder, 5 parts of porcelain calcium, 10 parts of bentonite, and 10 parts of rubber powder ; 80 parts of polyester resin, 25 parts of curing agent, 40 parts of zinc powder, 12 parts of antioxidant, 6 parts of benzoin, 4 parts of brightening agent.
[0029] A kind of processing method of powder coating, concrete method is as follows:
[0030] (1) All materials are weighed according to the proportion, after mixing;
[0031] (2) Extruded in a twin-screw extruder at about 120-135°C;
[0032] (3) The extruded tablet is crushed and passed through a 120-200 mesh sieve.
[0033] The zinc powder is selected from two mixtures of barium sulfate and titanium dioxide.
PUM
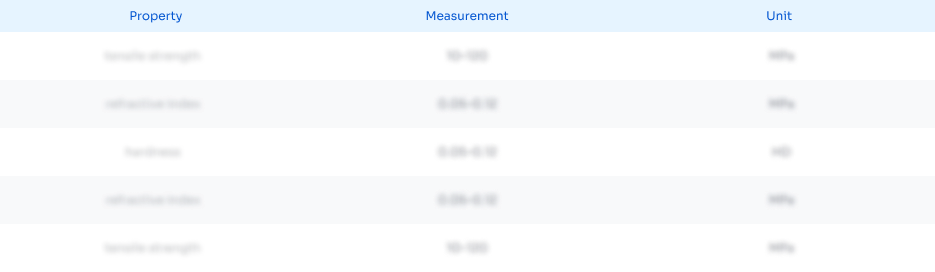
Abstract
Description
Claims
Application Information

- R&D Engineer
- R&D Manager
- IP Professional
- Industry Leading Data Capabilities
- Powerful AI technology
- Patent DNA Extraction
Browse by: Latest US Patents, China's latest patents, Technical Efficacy Thesaurus, Application Domain, Technology Topic, Popular Technical Reports.
© 2024 PatSnap. All rights reserved.Legal|Privacy policy|Modern Slavery Act Transparency Statement|Sitemap|About US| Contact US: help@patsnap.com