Lightweight design method for large-sized die-casting machine tail boards
A lightweight design, die-casting machine technology, applied in design optimization/simulation, calculation, multi-objective optimization, etc., can solve problems such as inability to effectively optimize design, complex force conditions, and difficult to obtain accurately. Process feasibility, effect of weight reduction, design and manufacturing cost reduction
- Summary
- Abstract
- Description
- Claims
- Application Information
AI Technical Summary
Problems solved by technology
Method used
Image
Examples
Embodiment Construction
[0026] like figure 1 As shown, a lightweight design method for a tail plate of a large-scale die-casting machine in the present invention includes the following steps: S1: Establish a three-dimensional assembly model of the clamping mechanism of a large-scale die-casting machine through CAD software.
[0027] S2: Read in the 3D assembly model of the mold clamping mechanism through the multi-body dynamics simulation software, establish a virtual prototype of the mold clamping mechanism of the die-casting machine, perform kinematics simulation on the virtual prototype model, and draw the effect of the tail plate and the machine hinge The force curve and the force curve of the straight hinge and the movable mold seat plate.
[0028] S3: Establish a discretized model of the tail plate of the die-casting machine through CAE software, take the force between the tail plate and the machine hinge as the input condition, conduct static stiffness analysis and modal analysis on the tail p...
PUM
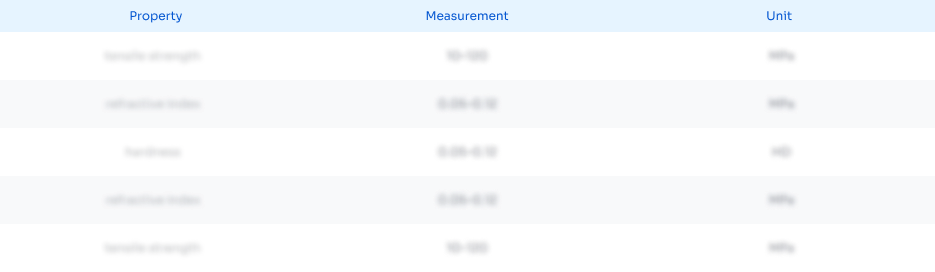
Abstract
Description
Claims
Application Information

- R&D
- Intellectual Property
- Life Sciences
- Materials
- Tech Scout
- Unparalleled Data Quality
- Higher Quality Content
- 60% Fewer Hallucinations
Browse by: Latest US Patents, China's latest patents, Technical Efficacy Thesaurus, Application Domain, Technology Topic, Popular Technical Reports.
© 2025 PatSnap. All rights reserved.Legal|Privacy policy|Modern Slavery Act Transparency Statement|Sitemap|About US| Contact US: help@patsnap.com