A kind of preparation method of thermoplastic polyurethane micro-airbag elastomer material
A thermoplastic polyurethane and elastomer material technology, applied in chemical instruments and methods, chemical/physical/physical-chemical stationary reactors, chemical/physical processes, etc., can solve the problems of low yield and high energy consumption
- Summary
- Abstract
- Description
- Claims
- Application Information
AI Technical Summary
Problems solved by technology
Method used
Image
Examples
preparation example Construction
[0052] A preparation method of thermoplastic polyurethane micro-airbag elastomer material, comprising the following steps:
[0053] (1) Feed liquid raw materials including diisocyanate molecules and polyols and solid additives into the twin-screw reactor for polymerization chain extension reaction to obtain high molecular weight hot melt;
[0054] (2), the high-molecular-weight hot melt of step (1) is pushed in the kneading extruder by twin-screw reactor outlet, continue to react, generate the high-molecular thermoplastic polyurethane melt of narrow molecular weight distribution;
[0055] (3), continue to feed the obtained polymer thermoplastic polyurethane melt into the foaming extruder, and at the same time, add polymer particle auxiliary materials, nucleating agents, and foaming agents to the foaming extruder to make the materials mix and distribute After uniformity, the melt booster pump controls the pressure and quantitatively transports it to the die head, and extrudes f...
Embodiment 1
[0077] According to the above as figure 1 The technical process prepares the heat loss type polyurethane micro-airbag elastomer material of the present invention according to the following raw material formula and process conditions:
[0078] Wherein, the polytetrahydrofuran ether glycol of preferred molecular weight 1000-2000 of polyol, adding weight ratio is 55-70%, diphenylmethane diisocyanate 20-35%, n-butanol 5-15%, hindered phenolic antioxidant ( Ciba Irganox 1010) 0.5-2%, hindered amine light stabilizer 0.5-2%, release agent 0.05-0.5%. The polymer chain extension reaction is carried out in the twin-screw reactor to produce a linear polyurethane macromolecular polymer with a molecular weight of 100,000 to 500,000. The heating temperature of the twin-screw reactor is 180-240°C, and the rotation speed is 100-1500rpm; the rotation speed of the mixing extruder is 100-300rpm, and the heating temperature is 140-220°C.
[0079] The polymer auxiliary material is the molecular ...
Embodiment 2
[0083] According to the above as figure 1 The technical process prepares the heat loss type polyurethane micro-airbag elastomer material of the present invention according to the following raw material formula and process conditions:
[0084] Wherein, the polytetrahydrofuran ether glycol of preferred molecular weight 1000 left and right of polyhydric alcohol, adding weight ratio is 55%, diphenylmethane diisocyanate 35%, n-butanol 5.5%, hindered phenolic antioxidant (Ciba Irganox1010) 2%, 2% hindered amine light stabilizer, 0.5% mold release agent. The polymer chain extension reaction is carried out in the twin-screw reactor to produce a linear polyurethane macromolecular polymer with a molecular weight of about 300,000. The heating temperature of the twin-screw reactor is 180°C, and the rotation speed is 800rpm; the rotation speed of the mixing extruder is 100rpm, and the heating temperature is 140°C.
[0085] The polymer auxiliary material is the molecular weight M w About...
PUM
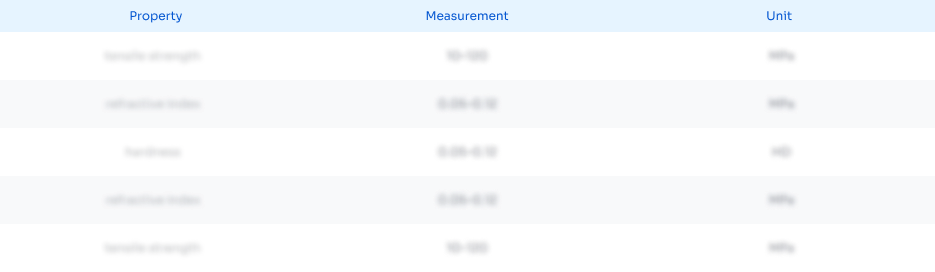
Abstract
Description
Claims
Application Information

- R&D
- Intellectual Property
- Life Sciences
- Materials
- Tech Scout
- Unparalleled Data Quality
- Higher Quality Content
- 60% Fewer Hallucinations
Browse by: Latest US Patents, China's latest patents, Technical Efficacy Thesaurus, Application Domain, Technology Topic, Popular Technical Reports.
© 2025 PatSnap. All rights reserved.Legal|Privacy policy|Modern Slavery Act Transparency Statement|Sitemap|About US| Contact US: help@patsnap.com