Processing method for wooden guitar
A processing method and guitar technology, which is applied to wood processing equipment, guitars, metal processing equipment, etc., can solve the problems of complicated guitar operation, achieve the effects of saving labor costs, improving the grinding effect, and ensuring consistency
- Summary
- Abstract
- Description
- Claims
- Application Information
AI Technical Summary
Problems solved by technology
Method used
Image
Examples
Embodiment 1
[0036] A kind of processing method of acoustic guitar of the present invention, comprises the steps:
[0037] A. Material selection: choose a whole piece of spruce and walnut with bright color and smooth surface to make the guitar top 3 and guitar side board respectively, and choose a whole mahogany core to make the guitar handle;
[0038] B. Drying: Use a dryer to dry the material in step A to a humidity of 5%-7% for subsequent cutting;
[0039] C. Cutting: Draw the contours of the guitar top and side panels on the spruce board and walnut board respectively, and use a cutting knife to cut out the blanks of the top and side boards along the 5mm outside the contour; cut the whole piece of mahogany into the body of the handle shape;
[0040] D. Grinding the shank and side plates: install the tool on the vertical shaft machine, and grind the shank and side plates;
[0041] E. Grinding the panel: use as figure 1 The sanding device shown sands the guitar top 3 as figure 1 A...
Embodiment 2
[0047] The difference between this embodiment and Embodiment 1 is that the fixing mechanism in the grinding device is different, such as figure 2 As shown, the fixing mechanism includes a baffle 6 arranged outside the grinding ball 4, a connecting rod 63 is connected between the baffle 6 and the upper frame 1, and an upper hook 62 and a lower hook 61 are welded between the two baffles 6. .
[0048] Sanding the panel includes the following steps:
[0049] a. Pull the baffle 6 from the upper splint 21 to both sides, pull the grinding ball 4 away from the upper splint 21, place the guitar panel 3 on the frame 1, and clamp the guitar with the upper splint 21 and the lower splint 2;
[0050] b. Attach the grinding ball 4 to the side of the panel, attach the baffle plate 6 to the outside of the grinding ball 4, hook the upper hook 62 and the lower hook 61 on the left side to the upper hook 62 and the lower hook 61 on the right side respectively, so that the baffle plate 6 Press...
PUM
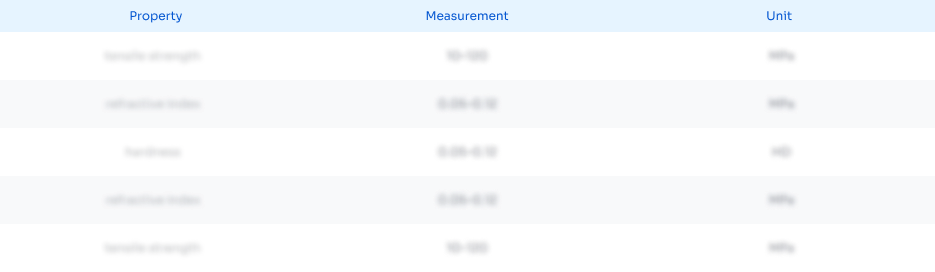
Abstract
Description
Claims
Application Information

- R&D
- Intellectual Property
- Life Sciences
- Materials
- Tech Scout
- Unparalleled Data Quality
- Higher Quality Content
- 60% Fewer Hallucinations
Browse by: Latest US Patents, China's latest patents, Technical Efficacy Thesaurus, Application Domain, Technology Topic, Popular Technical Reports.
© 2025 PatSnap. All rights reserved.Legal|Privacy policy|Modern Slavery Act Transparency Statement|Sitemap|About US| Contact US: help@patsnap.com