Welding process for ultrathin corrugated pipe
A welding process and bellows technology, which is applied in the field of bellows welding process to achieve the effect of reducing heat affected zone, reducing burn-through phenomenon and reducing welding deformation
Inactive Publication Date: 2017-11-24
JIANGSU BAOJINLAI PIPELINE EQUIP
View PDF6 Cites 0 Cited by
- Summary
- Abstract
- Description
- Claims
- Application Information
AI Technical Summary
Problems solved by technology
[0003] Aiming at the deficiencies of the prior art, the present invention proposes an ultra-thin corrugated pipe welding process that can significantly reduce the problems of easy burn-through and large welding deformation during welding
Method used
the structure of the environmentally friendly knitted fabric provided by the present invention; figure 2 Flow chart of the yarn wrapping machine for environmentally friendly knitted fabrics and storage devices; image 3 Is the parameter map of the yarn covering machine
View moreExamples
Experimental program
Comparison scheme
Effect test
Embodiment Construction
[0015] In the following, the present invention will be further described in conjunction with the embodiments.
[0016] The welding process of ultra-thin bellows includes the following steps:
[0017] 1) Choose an appropriate pressure plate;
[0018] 2) In the welding process, use reserved gap;
[0019] 3) A small welding heat input is adopted. In this embodiment, the welding heat input is 5.64 J / cm.
the structure of the environmentally friendly knitted fabric provided by the present invention; figure 2 Flow chart of the yarn wrapping machine for environmentally friendly knitted fabrics and storage devices; image 3 Is the parameter map of the yarn covering machine
Login to View More PUM
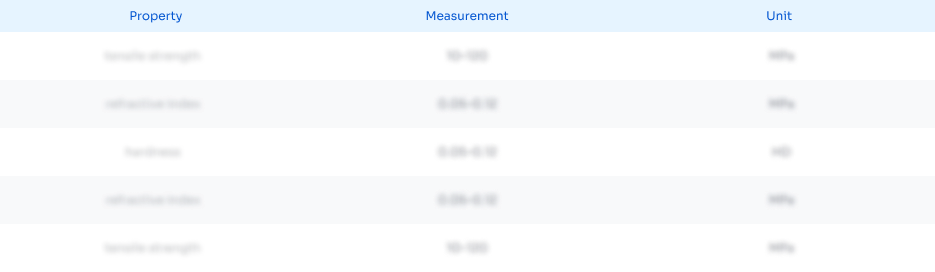
Abstract
The invention discloses a welding process for an ultrathin corrugated pipe. The process includes the following steps that (1) proper pressure of a pressing plate is selected; (2) a pre-welding gap is adopted in the course of welding; and (3) small welding line energy is adopted. The welding process is used for welding the ultrathin corrugated pipe, burnthrough cannot happen easily and welding deformation is small.
Description
Technical field [0001] The present invention relates to a welding process, in particular, the present invention relates to a bellows welding process. Background technique [0002] The wall thickness of the corrugated pipe is generally thin, and it is easy to burn through during welding, and the welding deformation is large, especially the ultra-thin corrugated pipe is more prone to the above problems. Summary of the invention [0003] Aiming at the deficiencies of the prior art, the present invention proposes an ultra-thin bellows welding process that can significantly reduce the problems of easy burn-through and large welding deformation that occur during welding. [0004] The present invention achieves the technical goals through the following technical solutions. [0005] The improvement of the ultra-thin bellows welding process is that it includes the following steps: [0006] 1) Choose an appropriate pressure plate; [0007] 2) In the welding process, use reserved gap; [0008] 3) ...
Claims
the structure of the environmentally friendly knitted fabric provided by the present invention; figure 2 Flow chart of the yarn wrapping machine for environmentally friendly knitted fabrics and storage devices; image 3 Is the parameter map of the yarn covering machine
Login to View More Application Information
Patent Timeline

Patent Type & Authority Applications(China)
IPC IPC(8): B23K31/02
CPCB23K31/027
Inventor 刘根喜
Owner JIANGSU BAOJINLAI PIPELINE EQUIP
Who we serve
- R&D Engineer
- R&D Manager
- IP Professional
Why Patsnap Eureka
- Industry Leading Data Capabilities
- Powerful AI technology
- Patent DNA Extraction
Social media
Patsnap Eureka Blog
Learn More Browse by: Latest US Patents, China's latest patents, Technical Efficacy Thesaurus, Application Domain, Technology Topic, Popular Technical Reports.
© 2024 PatSnap. All rights reserved.Legal|Privacy policy|Modern Slavery Act Transparency Statement|Sitemap|About US| Contact US: help@patsnap.com