An AC-DC five-degree-of-freedom dual-spherical hybrid magnetic bearing for a vehicle-mounted flywheel battery
A hybrid magnetic bearing and flywheel battery technology, which is applied in the direction of magnetic bearings, bearings, shafts, and bearings, can solve problems such as gyro effect and rotor mass aggravation, so as to suppress gyro effect, reduce friction and windage loss, reduce shaft effect on size
- Summary
- Abstract
- Description
- Claims
- Application Information
AI Technical Summary
Problems solved by technology
Method used
Image
Examples
Embodiment Construction
[0024] see figure 1 and figure 2 , the middle of the present invention is the rotor 7, and the outer coaxial sleeve of the rotor 7 has an axial stator 5 and a radial stator.
[0025] The radial stator is composed of an upper radial stator 1 and a lower radial stator 8 , and the upper radial stator 1 and the lower radial stator 8 are coaxially arranged along the axial direction of the rotor 7 . The yokes of the upper radial stator 1 and the lower radial stator 8 are coaxially arranged up and down along the axial direction of the rotor 7, and the upper and lower yokes are connected as a whole, and the upper and lower yokes form a hollow cylinder, and the inner cavity of the hollow cylinder That is, the radial stator pole cavity 16 .
[0026] The upper end surface of the upper radial stator 1 is flush with the upper end surface of the rotor 7 , and the lower end surface of the lower radial stator 8 is flush with the lower end surface of the rotor 7 .
[0027] In the radial st...
PUM
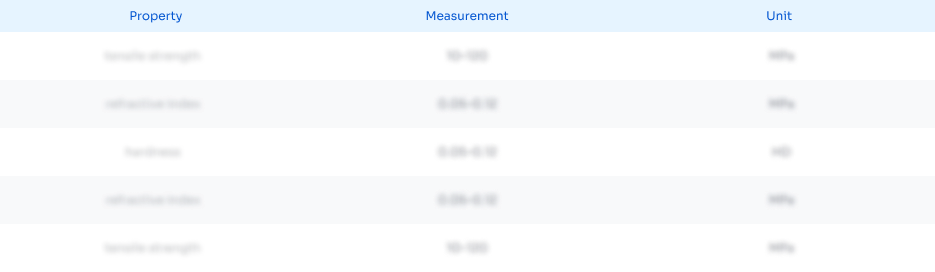
Abstract
Description
Claims
Application Information

- R&D
- Intellectual Property
- Life Sciences
- Materials
- Tech Scout
- Unparalleled Data Quality
- Higher Quality Content
- 60% Fewer Hallucinations
Browse by: Latest US Patents, China's latest patents, Technical Efficacy Thesaurus, Application Domain, Technology Topic, Popular Technical Reports.
© 2025 PatSnap. All rights reserved.Legal|Privacy policy|Modern Slavery Act Transparency Statement|Sitemap|About US| Contact US: help@patsnap.com