Inorganic thermal-insulation mortar and production method thereof
A technology of inorganic thermal insulation mortar and silica, applied in the direction of inorganic chemistry, chemical instruments and methods, non-metallic elements, etc., can solve the problems of affecting the thermal insulation effect of mortar, large shrinkage of thermal insulation mortar, high water absorption rate, etc., to improve the strength and Its impermeability, low density and high porosity effect
- Summary
- Abstract
- Description
- Claims
- Application Information
AI Technical Summary
Problems solved by technology
Method used
Image
Examples
example 1
[0029] Weigh 1.0kg of rice husk, wash it twice with deionized water, soak it in 2L hydrochloric acid with a mass fraction of 10%, and filter it after 3 hours to obtain the filter residue, wash the filter residue three times with deionized water, and then put the filter residue in a drying box , dried at 70°C for 8 hours to obtain pretreated rice husks, weighed 100g of pretreated rice husks, placed them in a resistance furnace, heated to 600°C at 10°C / min, kept the temperature for calcination for 1 hour, and cooled to room temperature to obtain rice husks ash, add rice husk ash to 1.5L sodium hydroxide solution with a mass fraction of 5%, in a constant temperature water bath at 90°C, stir at 300r / min for 2h, then filter and collect the filtrate to obtain a sodium silicate mixture. The mixed solution is ion-exchanged through a sodium ion exchange resin column at 10mL / min. After removing sodium ions, silicic acid sol is obtained. Add 10mL tetraethyl silicate and 8g aluminum silica...
example 2
[0031]Weigh 1.1kg of rice husk, wash it twice with deionized water, soak it in 2L hydrochloric acid with a mass fraction of 10%, and filter it after 4 hours to obtain a filter residue, wash the filter residue 4 times with deionized water, and then place the filter residue in a drying box , dried at 75°C for 9 hours to obtain pretreated rice husks, weighed 150g of pretreated rice husks, placed them in a resistance furnace, heated to 625°C at 13°C / min, kept the temperature for calcination for 1h, and cooled to room temperature to obtain rice husks ash, add rice husk ash to 1.8L of 5% sodium hydroxide solution, stir at 350r / min for 2 hours in a constant temperature water bath at 93°C, then filter and collect the filtrate to obtain a sodium silicate mixture. The mixed solution is ion-exchanged through a sodium ion exchange resin column at 11mL / min. After removing sodium ions, silicic acid sol is obtained. Add 11mL tetraethyl silicate and 9g aluminum silicate fiber to the silicic ac...
example 3
[0033] Weigh 1.2kg of rice husk, wash it with deionized water for 3 times, soak it in 3L of hydrochloric acid with a mass fraction of 10%, and filter it after 5 hours to obtain a filter residue, wash the filter residue with deionized water for 5 times, and then put the filter residue in a drying box , dried at 80°C for 10 hours to obtain pretreated rice husks, weighed 200g of pretreated rice husks, placed them in a resistance furnace, heated to 650°C at 15°C / min, kept the temperature for calcination for 2 hours, and cooled to room temperature to obtain rice husks ash, add rice husk ash to 2.0L of 5% sodium hydroxide solution, stir at 400r / min for 3 hours in a constant temperature water bath at 95°C, then filter and collect the filtrate to obtain a sodium silicate mixture. The mixed solution is ion-exchanged through a sodium ion exchange resin column at 12mL / min. After removing sodium ions, silicic acid sol is obtained. Add 12mL tetraethyl silicate and 10g aluminum silicate fibe...
PUM
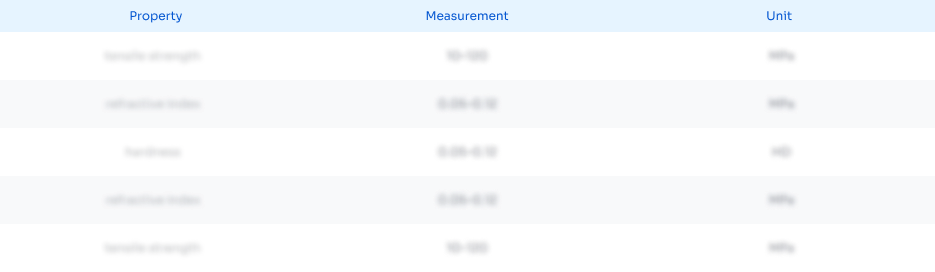
Abstract
Description
Claims
Application Information

- Generate Ideas
- Intellectual Property
- Life Sciences
- Materials
- Tech Scout
- Unparalleled Data Quality
- Higher Quality Content
- 60% Fewer Hallucinations
Browse by: Latest US Patents, China's latest patents, Technical Efficacy Thesaurus, Application Domain, Technology Topic, Popular Technical Reports.
© 2025 PatSnap. All rights reserved.Legal|Privacy policy|Modern Slavery Act Transparency Statement|Sitemap|About US| Contact US: help@patsnap.com