Structure applying the glass fiber-reinforced resin foam and manufacturing method therefor
A glass fiber and manufacturing method technology, applied in chemical instruments and methods, applications, synthetic resin layered products, etc., can solve problems such as delamination of surface and core material and decrease in toughness that have not been publicly solved, and achieve excellent physical properties, combined with Enhanced, small deflection effect
- Summary
- Abstract
- Description
- Claims
- Application Information
AI Technical Summary
Problems solved by technology
Method used
Image
Examples
Embodiment
[0075] 1. Phases S1 and S2
[0076] Figure 3a , 3b It is a cross-sectional view showing the manufacturing method in stages S1 to S2 of the manufacturing method of the carrier sandwich structure of the present invention. refer to Figure 3a , 3b , GCSM (Glass Continuous Strand Mat) consisting of glass continuous fibers was placed on a mold, and polyurethane was sprayed onto the GCSM.
[0077] 2. Stage S3
[0078] Figure 3c It is a cross-sectional view showing the manufacturing method at stage S3 of the manufacturing method of the carrier sandwich structure of the present invention. refer to Figure 3c , foaming the polyurethane by a reaction between the foamed polyurethane on the GCSM and the supplied blowing agent, thereby producing a foamed resin body.
[0079] 3. Stage S4
[0080] Figure 4 It is a cross-sectional view showing the manufacturing method at stage S4 of the manufacturing method of the carrier sandwich structure of the present invention. refer to F...
PUM
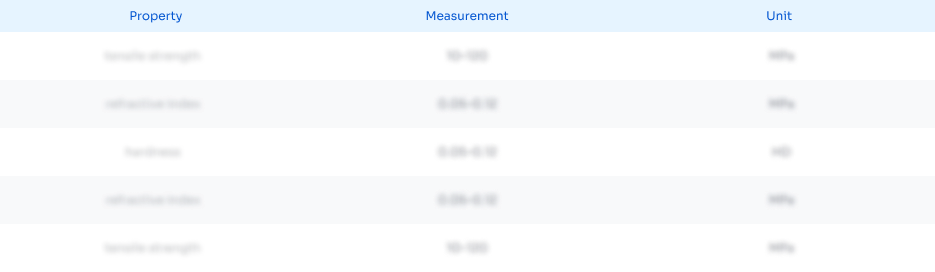
Abstract
Description
Claims
Application Information

- Generate Ideas
- Intellectual Property
- Life Sciences
- Materials
- Tech Scout
- Unparalleled Data Quality
- Higher Quality Content
- 60% Fewer Hallucinations
Browse by: Latest US Patents, China's latest patents, Technical Efficacy Thesaurus, Application Domain, Technology Topic, Popular Technical Reports.
© 2025 PatSnap. All rights reserved.Legal|Privacy policy|Modern Slavery Act Transparency Statement|Sitemap|About US| Contact US: help@patsnap.com