A kind of forging process of left axle shaft of automobile differential gear
An automotive differential and process technology, applied in the field of forging, can solve the problems affecting customer satisfaction, low product accuracy, long production cycle, etc., and achieve the effect of shortening production cycle, solving forging defects, and reducing blanking weight
- Summary
- Abstract
- Description
- Claims
- Application Information
AI Technical Summary
Problems solved by technology
Method used
Image
Examples
Embodiment 1
[0025] A forging process for the left axle shaft of an automobile differential, comprising the following steps:
[0026] (1) Blanking: Use a circular saw to cut the material, and the weight error of the material is controlled within ± 3g;
[0027] (2) Heating: heat the blank to 1100°C and keep it warm for 3 hours;
[0028] (3) Forming: Design the cavity of the free forging and elongating die to ensure that the cavity of the elongating die coincides with the cavity of the final forging die, and design a positioning device to be installed on the elongating die;
[0029] (4) trimming: use a press to remove excess flash;
[0030] (5) Quenching and tempering: heat the formed part to 1100°C, keep it warm for 4 hours, quickly put it in cold water to cool to 220°C, then raise it to 720°C, keep it warm for 6 hours, cool it to room temperature in the furnace, place it for 2 days, and then heat up again Heat at 750°C for 12 hours, then cool to room temperature in air;
[0031] (6) Sho...
Embodiment 2
[0036] A forging process for the left axle shaft of an automobile differential, comprising the following steps:
[0037] (1) Blanking: Use a circular saw to cut the material, and the weight error of the material is controlled within ± 3g;
[0038] (2) Heating: heat the blank to 1120°C and keep it warm for 4 hours;
[0039] (3) Forming: Design the cavity of the free forging and elongating die to ensure that the cavity of the elongating die coincides with the cavity of the final forging die, and design a positioning device to be installed on the elongating die;
[0040] (4) trimming: use a press to remove excess flash;
[0041] (5) Quenching and tempering: heat the formed part to 1050°C, keep it warm for 3 hours, quickly put it in cold water to cool to 200°C, then raise it to 750°C, keep it warm for 7 hours, cool it in the furnace to room temperature, place it for 1 day, and heat up again To 800°C, keep warm for 9h, and cool to room temperature in air;
[0042] (6) Shot blast...
Embodiment 3
[0047] A forging process for the left axle shaft of an automobile differential, comprising the following steps:
[0048] (1) Blanking: Use a circular saw to cut the material, and the weight error of the material is controlled within ± 3g;
[0049] (2) Heating: heat the blank to 1130°C and keep it warm for 3 hours;
[0050] (3) Forming: Design the cavity of the free forging and elongating die to ensure that the cavity of the elongating die coincides with the cavity of the final forging die, and design a positioning device to be installed on the elongating die;
[0051] (4) trimming: use a press to remove excess flash;
[0052] (5) Quenching and tempering: heat the formed part to 1150°C, keep it warm for 4 hours, quickly put it in cold water to cool to 300°C, then raise it to 600°C, keep it warm for 8 hours, cool it to room temperature in the furnace, place it for 2 days, and heat up again Heat at 760°C for 10 hours, then cool to room temperature in air;
[0053] (6) Shot bla...
PUM
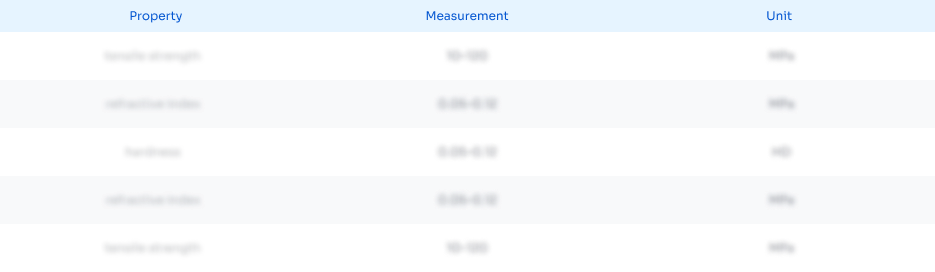
Abstract
Description
Claims
Application Information

- R&D
- Intellectual Property
- Life Sciences
- Materials
- Tech Scout
- Unparalleled Data Quality
- Higher Quality Content
- 60% Fewer Hallucinations
Browse by: Latest US Patents, China's latest patents, Technical Efficacy Thesaurus, Application Domain, Technology Topic, Popular Technical Reports.
© 2025 PatSnap. All rights reserved.Legal|Privacy policy|Modern Slavery Act Transparency Statement|Sitemap|About US| Contact US: help@patsnap.com