A prefabricated bamboo wood-concrete composite beam
A concrete and prefabricated technology, applied in the direction of joists, girders, trusses, etc., can solve the problems of difficult to give full play to the mechanical properties of connectors, low flexural rigidity and bearing capacity, difficult to control precise positioning, etc., to achieve a simple assembly method. , The effect of high bending rigidity and high production efficiency
- Summary
- Abstract
- Description
- Claims
- Application Information
AI Technical Summary
Problems solved by technology
Method used
Image
Examples
Embodiment Construction
[0027] As shown in the accompanying drawings, the present invention is an assembled bamboo-wood-concrete composite beam, comprising a prefabricated concrete slab (1), a bamboo-wood beam (2) and a steel pipe-ultra-high-performance concrete composite shear connector (3), prefabricated The concrete slab (1) and the bamboo beam (2) are combined through a steel pipe-ultra-high performance concrete composite shear connector (3); it is characterized in that: the steel pipe-ultra-high performance concrete composite shear connector (3) Including steel pipe (4), ultra-high performance concrete (5) and self-tapping screws (7), the steel pipe (4) is covered with ultra-high performance concrete (5), one end of the ultra-high performance concrete (5) is the connecting end, and the shape of the connecting end is It is a cylinder, and the other end of the ultra-high performance concrete (5) is an anchoring end, and the shape of the anchoring end is a circular platform; the prefabricated concre...
PUM
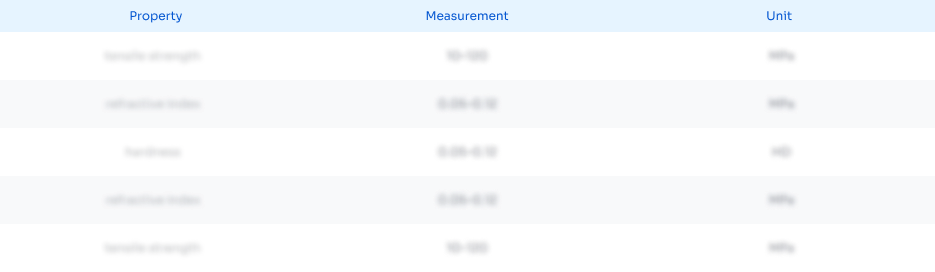
Abstract
Description
Claims
Application Information

- R&D
- Intellectual Property
- Life Sciences
- Materials
- Tech Scout
- Unparalleled Data Quality
- Higher Quality Content
- 60% Fewer Hallucinations
Browse by: Latest US Patents, China's latest patents, Technical Efficacy Thesaurus, Application Domain, Technology Topic, Popular Technical Reports.
© 2025 PatSnap. All rights reserved.Legal|Privacy policy|Modern Slavery Act Transparency Statement|Sitemap|About US| Contact US: help@patsnap.com