Automatic repair-grinding device for resistance spot-welding electrodes
A technology of resistance spot welding and dresser, which is applied in the direction of electrode characteristics, electrode maintenance, etc., can solve the problems of difficult to effectively control the excessive cutting of electrode materials, large edge impact, and strong edge impact, etc., to achieve the cost of use Low, grinding quality assurance, improve the effect of working life
- Summary
- Abstract
- Description
- Claims
- Application Information
AI Technical Summary
Problems solved by technology
Method used
Image
Examples
Embodiment Construction
[0074] The invention relates to a grinder specially used for automatic grinding of linear moving electrodes, electrodes including automatic welding tongs, manual welding tongs and fixed spot welding machines in the spot welding process. The electrode automatic grinder of the present invention realizes the precise control of the electrode grinding amount through the cutting mode controlled by the micro cutting amount and the positioning displacement in the electrode grinding process; The knife amount is determined by the displacement speed of the electrode surface to be repaired towards the cutting edge, and the displacement speed of the electrode to be repaired surface to the cutting edge is always controlled by the preset program in the dresser during the electrode grinding process. When the cutting tool grinds the electrode, it works in the form of revolution + rotation. The rotation axis of the revolution takes the electrode axis as the axis, that is, the connection line betwe...
PUM
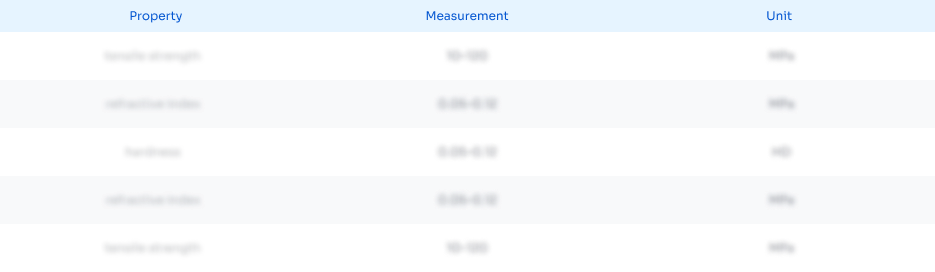
Abstract
Description
Claims
Application Information

- R&D
- Intellectual Property
- Life Sciences
- Materials
- Tech Scout
- Unparalleled Data Quality
- Higher Quality Content
- 60% Fewer Hallucinations
Browse by: Latest US Patents, China's latest patents, Technical Efficacy Thesaurus, Application Domain, Technology Topic, Popular Technical Reports.
© 2025 PatSnap. All rights reserved.Legal|Privacy policy|Modern Slavery Act Transparency Statement|Sitemap|About US| Contact US: help@patsnap.com