Method for producing and processing wool blended yarn
A technology of wool blending and processing methods, applied in yarn, textiles and papermaking, etc., can solve problems such as rising production costs, losing wool, and reducing the quality of final products, and achieve the effect of reducing production efficiency and reducing hairiness
- Summary
- Abstract
- Description
- Claims
- Application Information
AI Technical Summary
Problems solved by technology
Method used
Examples
Embodiment
[0016] A method for producing and processing wool blended yarn, comprising the following steps,
[0017] The first step is the selection of raw materials. The wool should be as long as possible, and the chemical fiber should be filament. The length of the wool should not be less than 65mm. The denier of the chemical fiber should be as small as possible, and should be controlled between 10D and 100D;
[0018] In the second step, the wool sliver goes through the process of blending, first needle combing, second needle combing, three needle carding, and four needle carding. The wool fibers are combined and then drafted to form a wool sliver. Try to be as straight as possible, and gradually thin the wool strips to the required grammage to form a roving. Among them, the combined number of mixed strips and first needle combs is not less than 8, and the draft ratio is not higher than 9 times. The combined number of two-way needle combs, three-way needle combs, and four-way needle com...
PUM
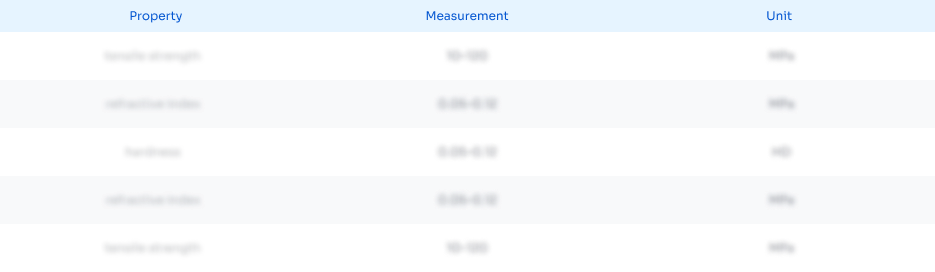
Abstract
Description
Claims
Application Information

- R&D Engineer
- R&D Manager
- IP Professional
- Industry Leading Data Capabilities
- Powerful AI technology
- Patent DNA Extraction
Browse by: Latest US Patents, China's latest patents, Technical Efficacy Thesaurus, Application Domain, Technology Topic, Popular Technical Reports.
© 2024 PatSnap. All rights reserved.Legal|Privacy policy|Modern Slavery Act Transparency Statement|Sitemap|About US| Contact US: help@patsnap.com