Method and device for film surface shaping
A film surface and thin film technology, applied in the field of film shaping, can solve the problems of inability to achieve shaping, elimination and improvement, leak coating, etc., and achieve the effects of meeting the shaping requirements, improving the shaping efficiency, and improving the flatness
- Summary
- Abstract
- Description
- Claims
- Application Information
AI Technical Summary
Problems solved by technology
Method used
Image
Examples
Embodiment 1
[0024] See figure 1 As shown, a device for film surface shaping provided in this embodiment includes a flattening heating roller 1 and a flattening cooling roller 2, and the flattening heating roller 1 is arranged on the side of the flattening cooling roller 2 The front end, and between the flattened heating roll 1 and the flattened cooling roll 2, a press roll A3 for breaking the tension is provided, and the rear end of the flattened cooling roll 2 is also provided with a press roll B4 for breaking the tension.
[0025] The film 5 is first heated and flattened by the flattening heating roller 1, and then the tension is cut by the pressure roller A3, and then cooled and shaped by the flattening cooling roller 2, and then wound up after the tension is cut by the pressure roller B4, that is, shaping After the membrane surface is flat film.
[0026] The temperature range for heating and flattening is preferably 30 to 85°C, and the temperature range for cooling and shaping is pre...
Embodiment 2
[0028] See figure 2 As shown, the difference between the device for film surface shaping provided in this embodiment and embodiment 1 is that the device for film surface shaping includes two flattening heating rollers 1 and two flattening cooling rollers 2 , and the direction of rotation of the two flattening heating rollers 1 is opposite, and the rotation direction of the two flattening cooling rollers 2 is opposite; the film 5 is passed through two flattening heating rollers 1, pressure roller A3, two flattening cooling rollers 2 and The pressure roller B 4 can make the front and back of the film can be heated, flattened and cooled to shape, not only the shaping effect is better, but also the shaping efficiency is higher.
[0029] In addition, the flattening heating roll in the present invention refers to a flattening roll with a heating function, which can be obtained by using the heating system of the heating roll and the roll surface shape of the flattening roll; the fla...
PUM
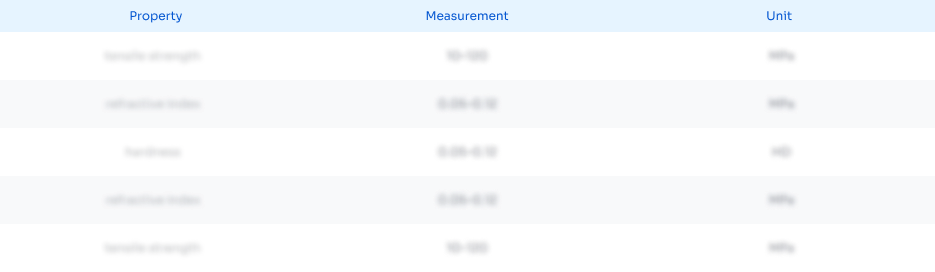
Abstract
Description
Claims
Application Information

- R&D
- Intellectual Property
- Life Sciences
- Materials
- Tech Scout
- Unparalleled Data Quality
- Higher Quality Content
- 60% Fewer Hallucinations
Browse by: Latest US Patents, China's latest patents, Technical Efficacy Thesaurus, Application Domain, Technology Topic, Popular Technical Reports.
© 2025 PatSnap. All rights reserved.Legal|Privacy policy|Modern Slavery Act Transparency Statement|Sitemap|About US| Contact US: help@patsnap.com