Full-prefabricated light steel assembled type composite wall plate capable of loading weight and manufacturing method thereof
A composite wall panel and assembly technology, which is applied in the direction of walls, buildings, building components, etc., can solve the problem of insufficient wall thermal insulation performance, vertical bearing capacity, horizontal shear capacity, and insufficient reliability of the vertical connection between the wall and the floor. The degree of assembly stays at the component level, slowing down the construction progress of the wall structure and other issues, achieving the effect of fast full prefabricated assembly construction, improving overall stability, and simple structure
- Summary
- Abstract
- Description
- Claims
- Application Information
AI Technical Summary
Problems solved by technology
Method used
Image
Examples
Embodiment Construction
[0025] like figure 1 , figure 2 , image 3 and Figure 4 As shown, a fully prefabricated and load-bearing light steel assembled composite wallboard, including light steel composite wallboard 1, transition patch board 2, upper U-shaped guide rail 3, lower U-shaped guide rail 4, cable-stayed steel belt 5, anti- Pull out the connector 6, fix the steel strip 7; the light steel composite wallboard 1 is a prefabricated lightweight polymer aggregate concrete wallboard with a standard structure with a C-shaped light steel frame inside the square structure, and the light steel composite wallboard The wall panel 1 is provided with raised grooves on the upper, lower, left and right sides, and the grooves contain a C-shaped light steel frame; The upper U-shaped guide rail 3 on the surface beam is fixedly connected, and the anti-pull connector 6 is connected and fixed between two adjacent standard light steel composite wall panels 1 by self-tapping screws 8, and the anti-pull connector...
PUM
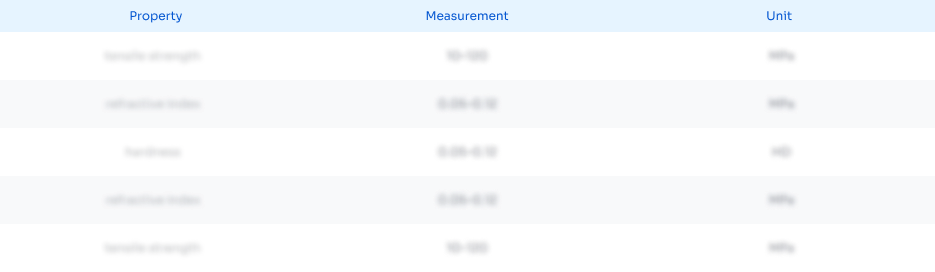
Abstract
Description
Claims
Application Information

- R&D Engineer
- R&D Manager
- IP Professional
- Industry Leading Data Capabilities
- Powerful AI technology
- Patent DNA Extraction
Browse by: Latest US Patents, China's latest patents, Technical Efficacy Thesaurus, Application Domain, Technology Topic, Popular Technical Reports.
© 2024 PatSnap. All rights reserved.Legal|Privacy policy|Modern Slavery Act Transparency Statement|Sitemap|About US| Contact US: help@patsnap.com