Steering knuckle molding process
A molding process and steering knuckle technology, applied in metal processing equipment, transportation and packaging, railway car body parts, etc., can solve the problems of large equipment investment, achieve high material utilization, improve product mechanical properties and corrosion resistance, The effect of simplifying the process
- Summary
- Abstract
- Description
- Claims
- Application Information
AI Technical Summary
Problems solved by technology
Method used
Image
Examples
Embodiment 1
[0028] A steering knuckle forming process includes the following steps:
[0029] (1) Cutting
[0030] The raw material inspection is first performed before cutting. The method of the raw material inspection is to detect the composition of the round steel blank of the steering knuckle, save the round steel blank after the inspection is passed, and then polish the round steel blank with sandpaper 2 After polishing, use dilute sulfuric acid to remove impurities on the surface of the round steel billet, then rinse it with distilled water for 1 min, dry it and perform sawing according to the size of the knuckle, the concentration of the dilute sulfuric acid is 30%;
[0031] (2) Heating
[0032] Place the blanked round steel billet in a double-hearth intermediate frequency induction furnace for heating. The double-hearth intermediate frequency induction furnace has a heating rate of 50°C / min, and the temperature of the double-hearth intermediate frequency induction furnace after heating is ...
Embodiment 2
[0044] A steering knuckle forming process includes the following steps:
[0045] (1) Cutting
[0046] The raw material inspection is first performed before cutting. The method of raw material inspection is to detect the composition of the round steel blank of the steering knuckle, store the round steel blank after the inspection is passed, and then sand the round steel blank with sandpaper 3 After polishing, use dilute sulfuric acid to remove impurities on the surface of the round steel billet, then rinse it with distilled water for 2 minutes, dry it and perform sawing according to the size of the knuckle. The concentration of the dilute sulfuric acid is 35%;
[0047] (2) Heating
[0048] The blanked round steel is placed in a double-hearth intermediate frequency induction furnace for heating. The double-hearth intermediate frequency induction furnace has a heating rate of 55°C / min, and the temperature of the double-hearth intermediate frequency induction furnace after heating is 1200...
Embodiment 3
[0060] A steering knuckle forming process includes the following steps:
[0061] (1) Cutting
[0062] The raw material inspection is first performed before cutting. The method of the raw material inspection is to detect the composition of the round steel blank of the steering knuckle, save the round steel blank after the inspection is passed, and then polish the round steel blank with sandpaper 4 After polishing, use dilute sulfuric acid to remove impurities on the surface of the round steel billet, then rinse it with distilled water for 2 minutes, dry it and perform sawing according to the size of the knuckle. The concentration of the dilute sulfuric acid is 40%;
[0063] (2) Heating
[0064] The round steel billet after blanking is placed in a double-hearth intermediate frequency induction furnace for heating. The double-hearth intermediate frequency induction furnace has a heating rate of 60°C / min, and the temperature of the double-hearth intermediate frequency induction furnace af...
PUM
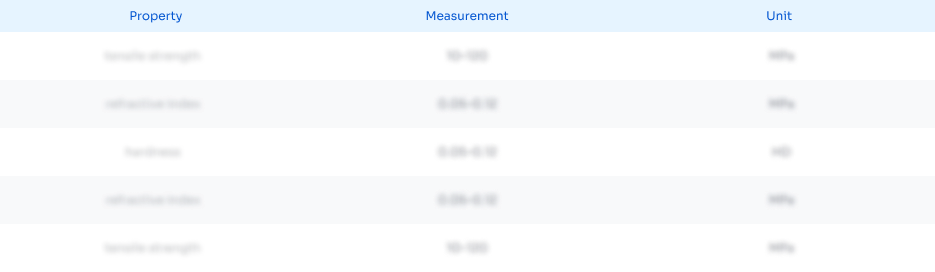
Abstract
Description
Claims
Application Information

- Generate Ideas
- Intellectual Property
- Life Sciences
- Materials
- Tech Scout
- Unparalleled Data Quality
- Higher Quality Content
- 60% Fewer Hallucinations
Browse by: Latest US Patents, China's latest patents, Technical Efficacy Thesaurus, Application Domain, Technology Topic, Popular Technical Reports.
© 2025 PatSnap. All rights reserved.Legal|Privacy policy|Modern Slavery Act Transparency Statement|Sitemap|About US| Contact US: help@patsnap.com