Preparation method of PVC (Polyvinyl Chloride) film for flex banner
A light box cloth and raw material preparation technology, applied in the field of plastic products, can solve the problems affecting the stretch resistance and fatigue resistance of PVC film, uneven dispersion, agglomeration stress, etc., to improve color uniformity, reasonable process settings, reduce The effect of stress concentration
- Summary
- Abstract
- Description
- Claims
- Application Information
AI Technical Summary
Problems solved by technology
Method used
Image
Examples
Embodiment 1
[0029] A preparation method of PVC film for light box cloth, comprising the steps of:
[0030] Raw material preparation: 60 parts of polyvinyl chloride resin, 50 parts of active nano-calcium carbonate, 8 parts of talcum powder, 25 parts of plasticizer, 3 parts of epoxy soybean oil, 3 parts of stabilizer, 1 part of active additive, 5 parts of auxiliary agent, 2.5 parts of colorant;
[0031] Pre-stirring treatment: put plasticizer, polyvinyl chloride resin and active nano-calcium carbonate in sequence in a kneader for high-temperature kneading to obtain a base material, wherein the kneading temperature is 100°C, and the kneading time is 30 minutes;
[0032] Pre-dispersion treatment: Put the base material obtained in the pre-stirring treatment step into the three-roll mill for two grinding and dispersion to obtain the dispersion base material;
[0033] High-speed stirring and mixing: Put the dispersed base material obtained in the pre-dispersion treatment step, epoxy soybean oil...
Embodiment 2
[0044] A preparation method of PVC film for light box cloth, comprising the steps of:
[0045] Raw material preparation: 80 parts of polyvinyl chloride resin, 60 parts of active nano-calcium carbonate, 10 parts of talcum powder, 40 parts of plasticizer, 5 parts of epoxy soybean oil, 5 parts of stabilizer, 3 parts of active additive, 7 parts of auxiliary agent, 3.5 parts of colorant;
[0046] Pre-stirring treatment: put plasticizer, polyvinyl chloride resin and active nano-calcium carbonate in sequence in a kneader for high-temperature kneading to obtain a base material, wherein the kneading temperature is 105°C, and the kneading time is 45 minutes;
[0047] Pre-dispersion treatment: Put the base material obtained in the pre-stirring treatment step into the three-roll mill for two grinding and dispersion to obtain the dispersion base material;
[0048]High-speed stirring and mixing: put the dispersed base material obtained in the pre-dispersion treatment step, epoxy soybean oi...
Embodiment 3
[0059] A preparation method of PVC film for light box cloth, comprising the steps of:
[0060] Raw material preparation: 70 parts of polyvinyl chloride resin, 50 parts of active nano-calcium carbonate, 8 parts of talcum powder, 30 parts of plasticizer, 4 parts of epoxy soybean oil, 4 parts of stabilizer, 2 parts of active additive, 5 parts of auxiliary agent, 3 parts of colorant;
[0061] Pre-stirring treatment: put plasticizer, polyvinyl chloride resin and active nano-calcium carbonate in sequence in a kneader for high-temperature kneading to obtain a base material, wherein the kneading temperature is 110°C, and the kneading time is 30 minutes;
[0062] Pre-dispersion treatment: Put the base material obtained in the pre-stirring treatment step into the three-roll mill for two grinding and dispersion to obtain the dispersion base material;
[0063] High-speed stirring and mixing: put the dispersed base material obtained in the pre-dispersion treatment step, epoxy soybean oil,...
PUM
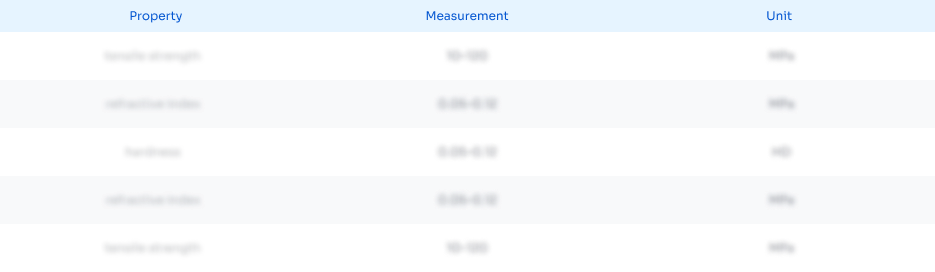
Abstract
Description
Claims
Application Information

- R&D Engineer
- R&D Manager
- IP Professional
- Industry Leading Data Capabilities
- Powerful AI technology
- Patent DNA Extraction
Browse by: Latest US Patents, China's latest patents, Technical Efficacy Thesaurus, Application Domain, Technology Topic, Popular Technical Reports.
© 2024 PatSnap. All rights reserved.Legal|Privacy policy|Modern Slavery Act Transparency Statement|Sitemap|About US| Contact US: help@patsnap.com