Coating material for electrostatic spraying on polypropylene automobile bumper bar
A polypropylene material, electrostatic spraying technology, used in polyester coatings, polyurea/polyurethane coatings, epoxy resin coatings, etc., can solve the problems of easy spattering, poor weather resistance, and can not meet the requirements of robotic electrostatic spraying, and achieves adaptation to Good performance and good paint film effect
- Summary
- Abstract
- Description
- Claims
- Application Information
AI Technical Summary
Problems solved by technology
Method used
Examples
Embodiment 1
[0032] The coating is made of the following components by weight: polyurethane resin ester 10, polyester resin 15, modified functional resin 20, ethyl acetate 5, butyl acetate 5, auxiliary agent 1, acrylic resin 8, resistance regulator 1, Color paste 35.
[0033] Preparation method steps:
[0034] (1) Synthesis of modified functional resin: Stir 30 parts of modified epoxy resin, 25 parts of modified amino resin, 35 parts of cellulose acetate butyrate solution, 8 parts of trimethylbenzene, and 2 parts of dispersant to obtain modified Functional resin, spare;
[0035] (2) Preparation of color paste: Weigh each raw material according to the following weight ratio: 60 parts of titanium dioxide, 10 parts of pigment, 5 parts of dispersant, 5 parts of wetting agent, 10 parts of silicon dioxide, 10 parts of trimethylbenzene, 400rpm After stirring evenly, stir again at 1600rpm for 5 minutes to obtain the pre-squeezing of the pigment; transfer the pre-smelting of the pigment to a sand...
Embodiment 2
[0041] The paint is made of the following components by weight: polyurethane resin ester 8, polyester resin 20, modified functional resin 28, ethyl acetate 10, butyl acetate 10, auxiliary agent 2, acrylic resin 5, resistance regulator 0.5, Color paste 30.
[0042] Preparation method steps:
[0043] (1) Synthesis of modified functional resin: Stir 25 parts of modified epoxy resin, 30 parts of modified amino resin, 40 parts of cellulose acetate butyrate solution, 14 parts of trimethylbenzene, and 1 part of dispersant to obtain modified Functional resin, spare;
[0044](2) Preparation of color paste: Weigh each raw material according to the following weight ratio: 50 parts of titanium dioxide, 15 parts of pigment, 8 parts of dispersant, 4 parts of wetting agent, 15 parts of silicon dioxide, 15 parts of trimethylbenzene, 800rpm After stirring evenly, stir again at 800rpm for 30 minutes to obtain the pre-squeezing of the pigment; transfer the pre-smelting of the pigment to a sand...
PUM
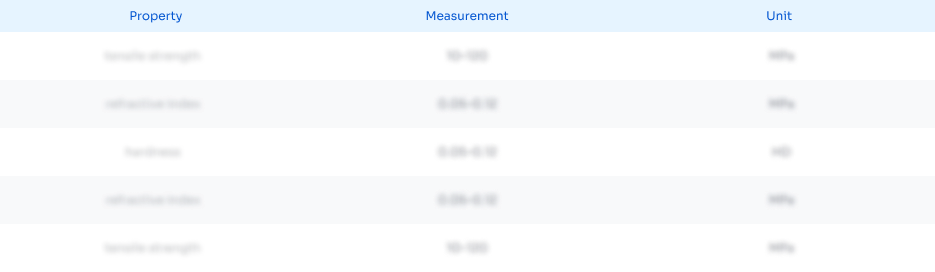
Abstract
Description
Claims
Application Information

- R&D
- Intellectual Property
- Life Sciences
- Materials
- Tech Scout
- Unparalleled Data Quality
- Higher Quality Content
- 60% Fewer Hallucinations
Browse by: Latest US Patents, China's latest patents, Technical Efficacy Thesaurus, Application Domain, Technology Topic, Popular Technical Reports.
© 2025 PatSnap. All rights reserved.Legal|Privacy policy|Modern Slavery Act Transparency Statement|Sitemap|About US| Contact US: help@patsnap.com