Multi-material micro-scale 3D printing device and printing method thereof
A 3D printing, micro-scale technology, applied in the field of additive manufacturing, to achieve the effect of simple production, material saving and cumbersome preparation process
- Summary
- Abstract
- Description
- Claims
- Application Information
AI Technical Summary
Problems solved by technology
Method used
Image
Examples
Embodiment 1
[0035] In a typical implementation of the present application, such as figure 1 As shown, a multi-material micro-scale 3D printing device is provided; including an electrohydrodynamic nozzle system and a working platform for mixing and printing a variety of materials;
[0036] The nozzle system includes a feeding device, a micro-mixing device, an ultraviolet curing lamp and a micro-nozzle, and the feeding device is provided with several micro-injection pumps and several feeding pipelines; the micro-mixing device is provided with A passive micro-mixer for effective mixing of materials with a high viscosity difference; the passive micro-mixer includes a liquid inlet flow channel, a mixing flow channel and a liquid outlet flow channel, and the number of the liquid inlet flow channels is not less than two, of which It is connected with the feeding pipeline of the feeding device, and the mixing flow channel is selected to have a flow channel structure that can effectively micro-mix...
Embodiment 2
[0044] figure 2 It is a schematic diagram of the principle of the passive micro-mixer in the nozzle system of the present invention, mainly including the liquid inlet flow channel 14, the mixing flow channel 15, and the liquid outlet flow channel 16; among them, multiple liquid inlet flow channels 14 can be selected to realize a variety of materials Micro-mixing, the mixing channel 15 selects a micro-mixer that can effectively mix high-viscosity difference liquids to achieve multi-ratio mixing of various materials, especially materials with different physical properties, such as the selection of mixing channels using sudden expansion The effect breaks the pressure balance at the fluid contact surface, and combines the split-recombination structure to induce the global fluid disturbance of the passive micro-mixer. The liquid outlet channel is connected to the micro-nozzle to provide micro-mixed and uniform micro-printed materials.
Embodiment 3
[0046] image 3 It is a schematic diagram of the preparation process of a micro-scale three-dimensional functionally graded structure device. First, the relevant software is used to optimize the gradient distribution of the material; then, the orthogonal experiment method is used to study the matching rules of the process parameters of mixed polymer micro-mixing, electrospray printing and deposition molding , set the relevant process parameters of each process; finally, multi-material micro-scale 3D printing is used to realize the preparation of micro-scale three-dimensional functionally graded structure devices. Specific steps are as follows:
[0047] Step 1: Perform cleaning and hydrophobic / hydrophilic coating treatment on the printed substrate 5. After cleaning the printed substrate, change its wetting characteristics by hydrophobic or hydrophilic treatment to realize the bottom surface morphology of the three-dimensional microstructure device. Effective control;
[0048]...
PUM
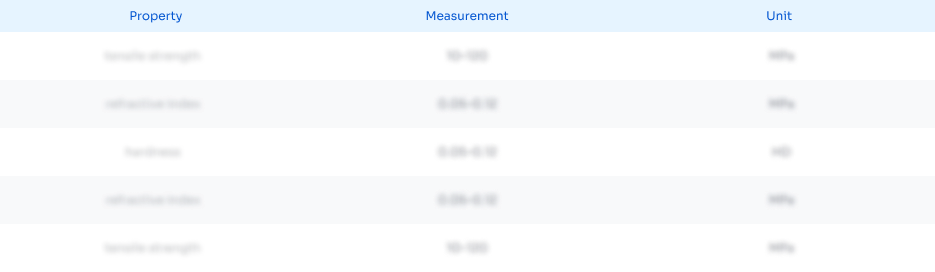
Abstract
Description
Claims
Application Information

- Generate Ideas
- Intellectual Property
- Life Sciences
- Materials
- Tech Scout
- Unparalleled Data Quality
- Higher Quality Content
- 60% Fewer Hallucinations
Browse by: Latest US Patents, China's latest patents, Technical Efficacy Thesaurus, Application Domain, Technology Topic, Popular Technical Reports.
© 2025 PatSnap. All rights reserved.Legal|Privacy policy|Modern Slavery Act Transparency Statement|Sitemap|About US| Contact US: help@patsnap.com