A Friction Stir Welding Method for Longitudinal Seam of Carrier Rocket Tank
A friction stir welding and launch vehicle technology, which is applied in welding equipment, non-electric welding equipment, attack equipment, etc., can solve the problem that the distance between the stirring needle and the back plate cannot be measured in real time, and achieve the effect of stable and reliable joint quality
- Summary
- Abstract
- Description
- Claims
- Application Information
AI Technical Summary
Problems solved by technology
Method used
Image
Examples
Embodiment Construction
[0026] In the present invention, the stirring head can adopt the structure shown in Table 1 when carrying out the friction stir welding of the longitudinal seam of the carrier rocket storage tank.
[0028]
[0030] Tank longitudinal seam friction stir welding adopts the welding sequence of formal welding after tack welding. Positioning welding adopts 5mm diameter stirrer
[0035] The diameter of the above-mentioned welding leakage groove 8 can be 6~10mm, and the depth can be 0.5~2mm.
[0038] The foregoing are only some embodiments of the present invention. It should be noted that for those of ordinary skill in the art
PUM
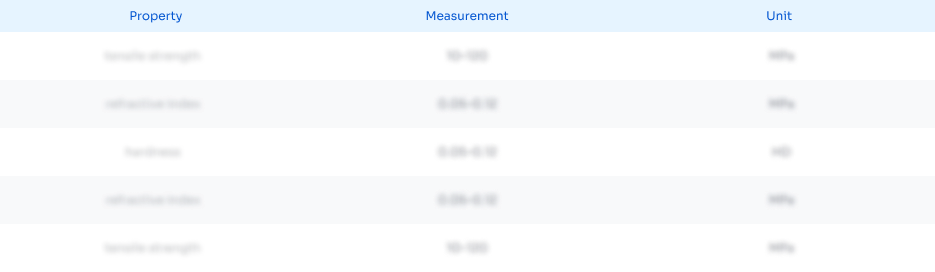
Abstract
Description
Claims
Application Information

- R&D Engineer
- R&D Manager
- IP Professional
- Industry Leading Data Capabilities
- Powerful AI technology
- Patent DNA Extraction
Browse by: Latest US Patents, China's latest patents, Technical Efficacy Thesaurus, Application Domain, Technology Topic, Popular Technical Reports.
© 2024 PatSnap. All rights reserved.Legal|Privacy policy|Modern Slavery Act Transparency Statement|Sitemap|About US| Contact US: help@patsnap.com