Graphene-containing polypropylene color master batch and preparation method thereof
A color masterbatch and polypropylene technology, applied in the field of graphene-containing polypropylene color masterbatch and its preparation, can solve problems such as inability to disperse well, and achieve the advantages of reducing the cost of raw materials, adding a small amount, and improving mechanical properties. Effect
- Summary
- Abstract
- Description
- Claims
- Application Information
AI Technical Summary
Problems solved by technology
Method used
Examples
Embodiment 1
[0042] 1. Add 26 parts of carbon black, 4 parts of graphene powder, and 18 parts of dispersant into the sand mill disperser, and grind at a speed of 1500 rpm. The average particle size of the grinding particles is controlled at 0.3-0.5 µm.
[0043] 2. Add 48 parts of polypropylene resin, 8 parts of ground material from step 1 and coupling agent into a low-speed mixer in sequence, and mix at room temperature for 2 to 5 minutes at 100 rpm. Add 3 parts of additives and 4 parts of high-temperature stabilizer to the mixture, and then use a high-speed mixer to mix at a high speed of 2000 rpm for 8-10 minutes.
[0044] 3. Transfer the mixture obtained in step 2 into a pressurized internal mixer, and pressurize and banbury under the conditions of 9-17kg pressure and 100-140°C for 15-25min.
[0045] 4. Plasticize and extrude the mixture after pressurized banburying with a screw extruder. The temperature settings of the five temperature zones in the extruder are 170°C, 180°C, 190°C, 180...
Embodiment 2
[0048] 1. Add 28 parts of carbon black, 5 parts of graphene powder, and 15 parts of dispersant into the sand mill disperser, and grind at a speed of 1500 rpm. The average particle size of the grinding particles is controlled at 0.3-0.5 µm.
[0049] 2. Add 50 parts of polypropylene resin, 6 parts of grinding material from step 1 and coupling agent into a low-speed mixer in sequence, and mix at room temperature for 2 to 5 minutes at 100 rpm. Add 3 parts of additives and 3 parts of high-temperature stabilizer to the mixture, and then use a high-speed mixer to mix at a high speed of 2000 rpm for 8-10 minutes.
[0050] 3. Transfer the mixture obtained in step 2 into a pressurized internal mixer, and pressurize and banbury under the conditions of 9-17kg pressure and 100-140°C for 15-25min.
[0051] 4. Plasticize and extrude the mixture after pressurized banburying with a screw extruder. The temperature settings of the five temperature zones in the extruder are 170°C, 180°C, 190°C, 1...
Embodiment 3
[0054] 1. Add 28 parts of carbon black, 4 parts of graphene powder, and 21 parts of dispersant into the sand mill disperser, and grind at a speed of 1500 rpm. The average particle size of the grinding particles is controlled at 0.3-0.5 µm.
[0055] 2. Add 55 parts of polypropylene resin, 7 parts of grinding material from step 1 and 7 parts of coupling agent into the low-speed mixer in sequence, and mix at room temperature for 2 to 5 minutes at 100 rpm. Add 4 parts of additives and 4 parts of high-temperature stabilizer to the mixture, and then use a high-speed mixer to mix at a high speed of 2000 rpm for 8-10 minutes.
[0056] 3. Transfer the mixture obtained in step 2 into a pressurized internal mixer, and pressurize and banbury under the conditions of 9-17kg pressure and 100-140°C for 15-25min.
[0057] 4. Plasticize and extrude the mixture after pressurized banburying with a screw extruder. The temperature settings of the five temperature zones in the extruder are 170°C, 18...
PUM
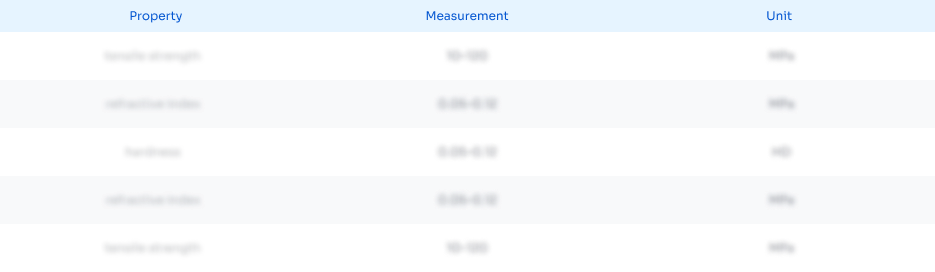
Abstract
Description
Claims
Application Information

- Generate Ideas
- Intellectual Property
- Life Sciences
- Materials
- Tech Scout
- Unparalleled Data Quality
- Higher Quality Content
- 60% Fewer Hallucinations
Browse by: Latest US Patents, China's latest patents, Technical Efficacy Thesaurus, Application Domain, Technology Topic, Popular Technical Reports.
© 2025 PatSnap. All rights reserved.Legal|Privacy policy|Modern Slavery Act Transparency Statement|Sitemap|About US| Contact US: help@patsnap.com