Brake pad steel backing precision stamping die assembly
A technology of mold assembly and brake pads, which is applied in the field of stamping manufacturing, can solve the problems of increased production costs, low integration of processing links, and incoherent production steps, etc., and achieves the effects of convenient operation, improved production efficiency, and reduced production processes
- Summary
- Abstract
- Description
- Claims
- Application Information
AI Technical Summary
Problems solved by technology
Method used
Image
Examples
Embodiment Construction
[0021] The structure and working principle of a brake pad steel back fine-blanking die assembly provided by the present invention will be further described in detail below in conjunction with the accompanying drawings.
[0022] Such as figure 1 As shown, it is a kind of brake pad steel back fine blanking die assembly provided by the present invention
[0023] Schematic. The structure constituting the brake pad steel back fine blanking die assembly is mainly composed of an upper die 1 provided with a punch 11 and a lower die 2 provided with a die 21, wherein the upper die 1 includes an upper die backing plate 12 and a The upper die is installed with a base plate 13, and the upper part of the upper die backing plate 12 is used to accept the downward fine blanking pressure. The punch 11 is arranged on the lower part of the upper die installed base plate 13 through the punch mounting plate 110; the lower die 2 includes a lower die base 22 and The lower die backing plate 23 conne...
PUM
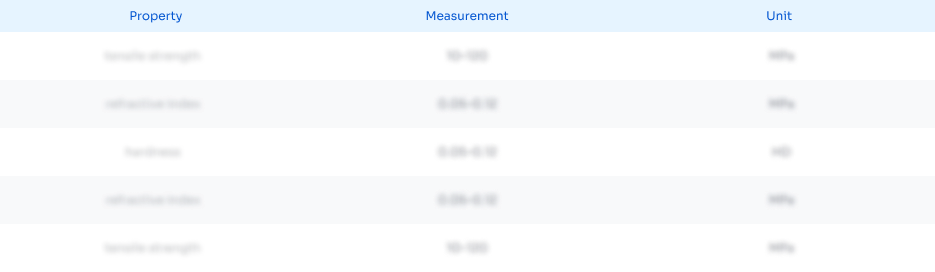
Abstract
Description
Claims
Application Information

- R&D Engineer
- R&D Manager
- IP Professional
- Industry Leading Data Capabilities
- Powerful AI technology
- Patent DNA Extraction
Browse by: Latest US Patents, China's latest patents, Technical Efficacy Thesaurus, Application Domain, Technology Topic, Popular Technical Reports.
© 2024 PatSnap. All rights reserved.Legal|Privacy policy|Modern Slavery Act Transparency Statement|Sitemap|About US| Contact US: help@patsnap.com