Copper foil substrate preparation method and metamaterial processing method using same
A technology of metamaterials and base materials, which is applied in the manufacture of printed circuits, printed circuit precursors, electrical components, etc., can solve the problems of restricting the production requirements of precision microstructures, difficult processing, and high costs, and achieve the expansion of the scope of availability, Reduce material cost and solve the effect of high cost
- Summary
- Abstract
- Description
- Claims
- Application Information
AI Technical Summary
Problems solved by technology
Method used
Image
Examples
Embodiment Construction
[0026] In order to enable those skilled in the art to better understand the solutions of the present invention, the following will clearly and completely describe the technical solutions in the embodiments of the present invention in conjunction with the drawings in the embodiments of the present invention. Obviously, the described embodiments are only It is an embodiment of a part of the present invention, but not all embodiments. Based on the embodiments of the present invention, all other embodiments obtained by persons of ordinary skill in the art without making creative efforts shall fall within the protection scope of the present invention.
[0027] Such as figure 1 Shown, a kind of copper foil substrate preparation method of the present invention comprises the following steps:
[0028] S1: Copper thickness reduction by vacuum etching;
[0029] Copper thickness is uniformly reduced by vacuum etching for multiple copper foil substrates of common thickness. In the proce...
PUM
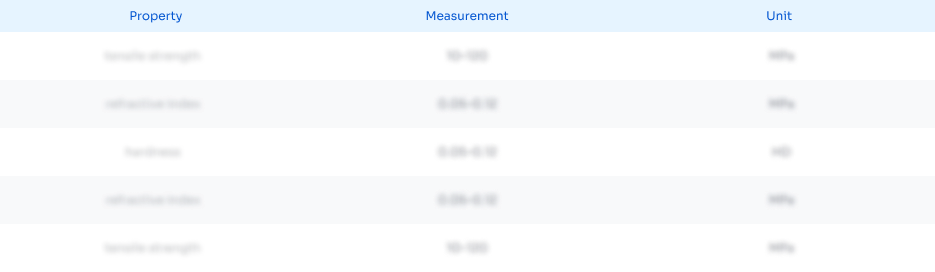
Abstract
Description
Claims
Application Information

- Generate Ideas
- Intellectual Property
- Life Sciences
- Materials
- Tech Scout
- Unparalleled Data Quality
- Higher Quality Content
- 60% Fewer Hallucinations
Browse by: Latest US Patents, China's latest patents, Technical Efficacy Thesaurus, Application Domain, Technology Topic, Popular Technical Reports.
© 2025 PatSnap. All rights reserved.Legal|Privacy policy|Modern Slavery Act Transparency Statement|Sitemap|About US| Contact US: help@patsnap.com