Magnetic composite bentonite and preparation method of same
A technology of bentonite and magnetism, which is applied in the field of modification and preparation of bentonite for water treatment, can solve the problems of fine bentonite particles, difficulties in practical application, and increased amount of sludge, and achieves improved superparamagnetism, simple and feasible preparation process, and low preparation cost Effect
- Summary
- Abstract
- Description
- Claims
- Application Information
AI Technical Summary
Problems solved by technology
Method used
Examples
Embodiment 1
[0021] A magnetic composite bentonite, prepared from the following raw materials in parts by weight: 40-50 parts of bentonite, 20-25 parts of iron oxide, 2-3 parts of ferric chloride, 2-3 parts of iron sulfate, 2-3 parts of polyaluminum sulfate 3 parts, 2-3 parts of activated carbon, 0.1-0.3 parts of dodecyl quaternary ammonium salt.
[0022] A preparation method of magnetic composite bentonite, comprising:
[0023] S1. Add bentonite, ferric oxide, ferric chloride and ferric sulfate to ethylene glycol at 65° C. under nitrogen, and stir for 2 hours;
[0024] S2. Put the mixed liquid obtained in step 1 in a polytetrafluoroethylene reactor, and react at 180° C. for 10 hours to obtain a black solid;
[0025] S3. Wash the black solid with distilled water, add activated carbon, polyaluminum sulfate, and dodecyl quaternary ammonium salt solution, and stir for 12 hours to obtain magnetic bentonite;
[0026] S4. Drying the magnetic bentonite at 70° C. and pulverizing it to 300 mesh t...
Embodiment 2
[0029] A magnetic composite bentonite, prepared from the following raw materials in parts by weight: 40-50 parts of bentonite, 20-25 parts of iron oxide, 2-3 parts of ferric chloride, 2-3 parts of iron sulfate, 2-3 parts of polyaluminum sulfate 3 parts, 2-3 parts of activated carbon, 0.1-0.3 parts of dodecyl quaternary ammonium salt.
[0030] A preparation method of magnetic composite bentonite, comprising:
[0031] S1. Add bentonite, ferric oxide, ferric chloride, and ferric sulfate to ethylene glycol at 75°C under inert gas conditions, and stir for 1 hour;
[0032] S2. Put the mixed liquid obtained in step 1 in a polytetrafluoroethylene reactor, and react at 200° C. for 8 hours to obtain a black solid;
[0033] S3. Wash the black solid with distilled water, add activated carbon, polyaluminum sulfate, and dodecyl quaternary ammonium salt, and stir for 24 hours to obtain magnetic bentonite;
[0034] S4. Drying the magnetic bentonite at 90° C. and pulverizing it to 500 mesh t...
Embodiment 3
[0037] A magnetic composite bentonite, prepared from the following raw materials in parts by weight: 50-60 parts of bentonite, 25-30 parts of iron oxide, 3-4 parts of ferric chloride, 2-3 parts of iron sulfate, 2-3 parts of polyaluminum sulfate 3 parts, 3-4 parts of activated carbon, 0.3-0.8 parts of dodecyl quaternary ammonium salt.
[0038] A preparation method of magnetic composite bentonite, comprising:
[0039] S1. Add bentonite, ferric oxide, ferric chloride and ferric sulfate to ethylene glycol at 65° C. under nitrogen, and stir for 2 hours;
[0040] S2. Put the mixed solution obtained in step 1 in a polytetrafluoroethylene reactor, and react at 180° C. for 10 hours to obtain a black solid;
[0041] S3. Wash the black solid with distilled water, add activated carbon, polyaluminum sulfate, and dodecyl quaternary ammonium salt solution, and stir for 12 hours to obtain magnetic bentonite;
[0042] S4. Drying the magnetic bentonite at 70° C. and pulverizing it to 300 mesh...
PUM
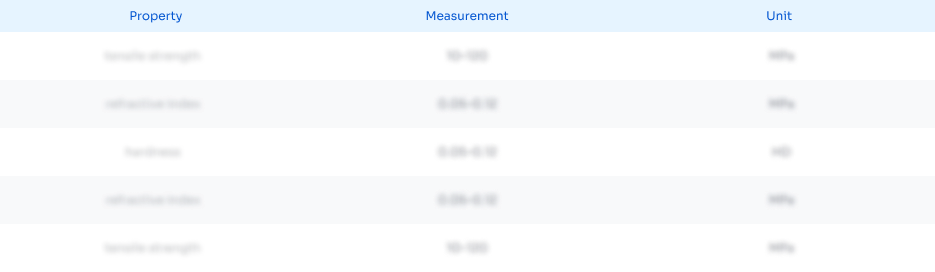
Abstract
Description
Claims
Application Information

- R&D
- Intellectual Property
- Life Sciences
- Materials
- Tech Scout
- Unparalleled Data Quality
- Higher Quality Content
- 60% Fewer Hallucinations
Browse by: Latest US Patents, China's latest patents, Technical Efficacy Thesaurus, Application Domain, Technology Topic, Popular Technical Reports.
© 2025 PatSnap. All rights reserved.Legal|Privacy policy|Modern Slavery Act Transparency Statement|Sitemap|About US| Contact US: help@patsnap.com