Electric spindle capable of realizing automatic tool changing and provided with build-in shank
An automatic tool change and built-in technology, which is applied in the direction of metal processing machinery parts, maintenance and safety accessories, metal processing equipment, etc., can solve the problem that the radial machining accuracy and processing efficiency are difficult to guarantee at the same time, affecting the working efficiency and service life of the spindle , Inability to realize online automatic tool change and other problems, to achieve the effects of increased structural strength, reduced maintenance costs, and reduced rolling and sliding friction
- Summary
- Abstract
- Description
- Claims
- Application Information
AI Technical Summary
Problems solved by technology
Method used
Image
Examples
specific Embodiment approach
[0028] Such as Figure 1-8 As shown, an electric spindle with a built-in tool holder for automatic tool change includes a main shaft body 1 and a drive device 2 that provides power and is transmission-connected to the main shaft body 1. The main shaft body 1 is provided with a cooling mechanism 3. The spindle body 1 includes a spindle housing 5 with a spindle assembly 4 press-fitted therein, a rear seat 6 and a dust cover 7 respectively arranged at both ends of the spindle housing 5, and the spindle assembly 4 is fixedly installed through a cooling copper sleeve 8 In the spindle housing 5, the rear seat 6 is provided with a detection device 9 and a control device, one end of the spindle assembly 4 is connected to the driving device 2 in a transmission manner, and the other end is detachably connected to the knife The handle 10 is connected.
[0029] Wherein, the two ends of the main shaft body 1 respectively include a rear bearing assembly 11, a front bearing assembly 12 and ...
PUM
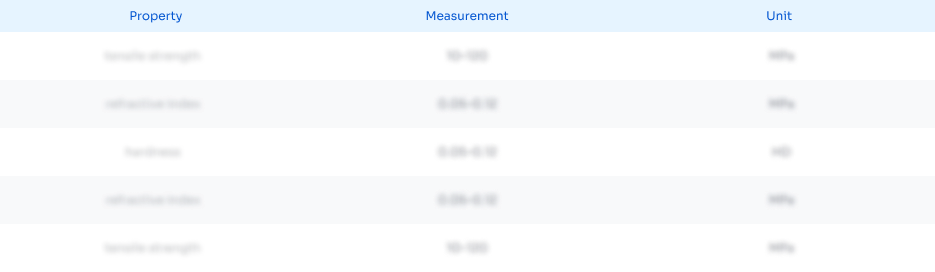
Abstract
Description
Claims
Application Information

- R&D
- Intellectual Property
- Life Sciences
- Materials
- Tech Scout
- Unparalleled Data Quality
- Higher Quality Content
- 60% Fewer Hallucinations
Browse by: Latest US Patents, China's latest patents, Technical Efficacy Thesaurus, Application Domain, Technology Topic, Popular Technical Reports.
© 2025 PatSnap. All rights reserved.Legal|Privacy policy|Modern Slavery Act Transparency Statement|Sitemap|About US| Contact US: help@patsnap.com