Preparation method of flame-retardant composite through dynamic vulcanization
A technology of flame-retardant composite materials and dynamic vulcanization, which is applied in the field of material preparation to reduce costs, improve flame-retardant performance, and meet the effects of flame-retardant performance
- Summary
- Abstract
- Description
- Claims
- Application Information
AI Technical Summary
Problems solved by technology
Method used
Examples
Embodiment 1
[0017] A method for preparing a dynamically vulcanized flame-retardant composite material, comprising the steps of:
[0018] (1) Vacuum dry PP, EPDM and Mg(OH)2 respectively;
[0019] (2) Add the mixture of PP and EPDM to the torque rheometer and banbury for 5 minutes. After the torque is balanced, add the crosslinking agent dicumyl peroxide DCP and banbury for 5 minutes until the torque is balanced. Finally, add the flame retardant and banbury Halogen-free flame retardant dynamically vulcanized blends up to torque balance;
[0020] (3) Put the halogen-free flame-retardant dynamic vulcanization blend into a compression molding machine, set the temperature at 150°C, press at 10MPa for 15 minutes, take it out, and then cold press at 5MPa to complete the preparation.
[0021] The preparation method of the dynamic vulcanization flame-retardant composite material of the present invention, described PP, EPDM, Mg(OH) 2 The matching ratio is 80, 20, 80, 1.0.
[0022] In the prepara...
Embodiment 2
[0031] A method for preparing a dynamically vulcanized flame-retardant composite material, comprising the steps of:
[0032] (1) Combine PP, EPDM and Mg(OH) 2 Carry out vacuum drying respectively;
[0033] (2) Add the mixture of PP and EPDM to the torque rheometer and banbury for 5 minutes. After the torque is balanced, add the crosslinking agent dicumyl peroxide DCP and banbury for 5 minutes until the torque is balanced. Finally, add the flame retardant and banbury Halogen-free flame retardant dynamically vulcanized blends up to torque balance;
[0034] (3) Put the halogen-free flame-retardant dynamic vulcanization blend into the compression molding machine, set the temperature at 190°C, press at 10MPa for 15 minutes, take it out, and then cold press at 5MPa to complete the preparation.
[0035] The preparation method of the dynamic vulcanization flame-retardant composite material of the present invention, described PP, EPDM, Mg(OH) 2 The matching ratio is 80, 20, 80, 1.0....
PUM
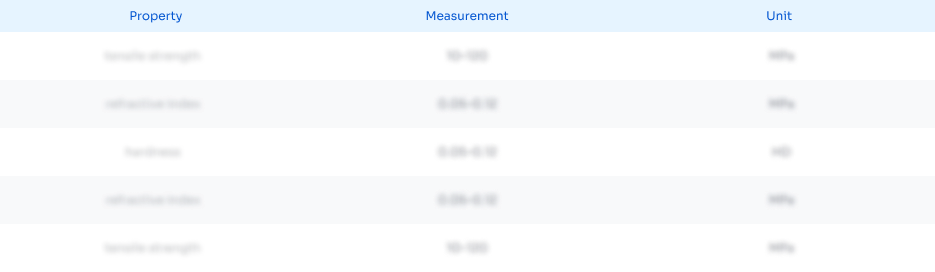
Abstract
Description
Claims
Application Information

- Generate Ideas
- Intellectual Property
- Life Sciences
- Materials
- Tech Scout
- Unparalleled Data Quality
- Higher Quality Content
- 60% Fewer Hallucinations
Browse by: Latest US Patents, China's latest patents, Technical Efficacy Thesaurus, Application Domain, Technology Topic, Popular Technical Reports.
© 2025 PatSnap. All rights reserved.Legal|Privacy policy|Modern Slavery Act Transparency Statement|Sitemap|About US| Contact US: help@patsnap.com