A method for preparing maleic anhydride through continuous dehydration of maleic acid
A technology of maleic acid and maleic anhydride, applied in the direction of organic chemistry, can solve problems such as product quality reduction, pipeline and equipment blockage, energy consumption safety, environmental protection, etc., and achieve the effects of improving efficiency, reducing production costs, and reducing energy consumption
- Summary
- Abstract
- Description
- Claims
- Application Information
AI Technical Summary
Problems solved by technology
Method used
Examples
Embodiment 1
[0028] Adopt the glass rectifying tower of diameter 30mm as dehydration equipment, tower height 1.5m, be the citric acid aqueous solution feeding place apart from tower still 1.2m place, be xylene and acetic anhydride feeding place (xylene and acetic anhydride feed place apart from tower still 0.3m place) The feed inlet of acetic anhydride is different);
[0029] Add 200ml of xylene and 10ml of acetic anhydride to the tower kettle, and heat it to reflux at normal pressure. At this time, the temperature of the kettle is 142°C, and the top temperature is 136°C. Start to continuously pump in an aqueous solution containing 30% of citric acid, xylene and acetic anhydride. The feed rate of acid aqueous solution is 60ml / hr, the feed rate of xylene is 180ml / hr, and the feed rate of acetic anhydride is 20ml / hr. At the same time, the reflux ratio at the top of the tower is 8, and the oil-water ratio is 2.5:1. The top temperature is 94.5°C, and after 6 hours of experimentation, there is ...
Embodiment 2
[0032] A glass rectification tower with a diameter of 30mm is used as the dehydration equipment. The height of the tower is 1.5m. The place 1.2m away from the tower kettle is the feeding place of the citric acid aqueous solution, the place 0.3m away from the tower kettle is the feeding place of xylene, and the place 0.2m away from the tower kettle It is the feeding place of acetic anhydride;
[0033] Add 200ml of xylene and 20ml of acetic anhydride to the tower kettle, and heat it to reflux at normal pressure. At this time, the temperature of the kettle is 142°C, and the top temperature is 136°C. Start to continuously pump in the aqueous solution containing 30% citric acid, xylene and acetic anhydride, and the cis The feed rate of acid aqueous solution is 60ml / hr, the feed rate of xylene is 180ml / hr, and the feed rate of acetic anhydride is 20ml / hr. At the same time, the reflux ratio at the top of the tower is 8, and the oil-water ratio is 2.5:1. The top temperature is 94.5°C,...
Embodiment 3
[0036] A glass rectification tower with a diameter of 30mm is used as the dehydration equipment. The height of the tower is 1.5m. The place 1.2m away from the tower kettle is the feeding place of the citric acid aqueous solution, the place 0.3m away from the tower kettle is the feeding place of xylene, and the place 0.2m away from the tower kettle It is the feeding place of acetic anhydride;
[0037] Add 200ml of xylene and 20ml of acetic anhydride to the tower kettle, and heat it to reflux at normal pressure. At this time, the temperature of the kettle is 142°C, and the top temperature is 136°C. Start to continuously pump in an aqueous solution containing 30% of citric acid, xylene and acetic anhydride to Feed rate is 60ml / hr, xylene feed rate is 180ml / hr, acetic anhydride feed rate is 20ml / hr, while the tower top adopts a reflux ratio of 1, and the production oil-water ratio is a cut of 2.5:1. At this time, the tower top temperature The temperature was 94.5°C, and after 6 ho...
PUM
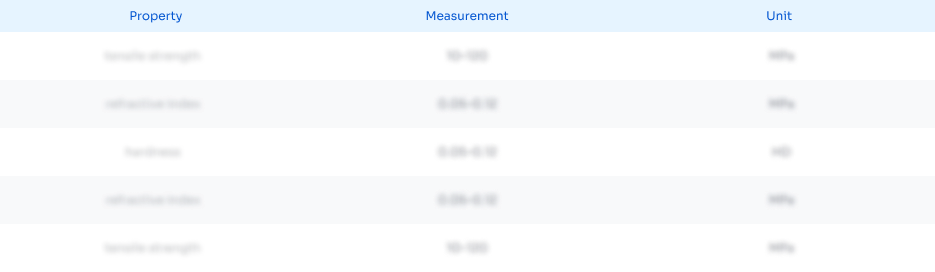
Abstract
Description
Claims
Application Information

- R&D Engineer
- R&D Manager
- IP Professional
- Industry Leading Data Capabilities
- Powerful AI technology
- Patent DNA Extraction
Browse by: Latest US Patents, China's latest patents, Technical Efficacy Thesaurus, Application Domain, Technology Topic, Popular Technical Reports.
© 2024 PatSnap. All rights reserved.Legal|Privacy policy|Modern Slavery Act Transparency Statement|Sitemap|About US| Contact US: help@patsnap.com