Method for processing wood fibers by plasma for reinforcing interface bonding capacity of fiber plate
A plasma and wood fiber technology, applied in wood treatment, electric wood treatment, wood treatment details, etc., can solve the problems of formaldehyde harmful to health, weak bonding ability of wood fiber/lignin interface, waste water pollution, etc., and achieve short treatment cycle , good gluing effect and low energy consumption
- Summary
- Abstract
- Description
- Claims
- Application Information
AI Technical Summary
Problems solved by technology
Method used
Examples
specific Embodiment approach 1
[0023] Specific embodiment one: a kind of method that utilizes plasma to improve wood fiber and lignin to strengthen the interfacial bonding performance described in this embodiment is specifically carried out according to the following steps:
[0024] One, select an appropriate amount of wood fiber, place it in an oven to dry, and obtain wood fiber with a certain moisture content (12%-16%);
[0025] 2. Open the plasma generator reactor, and evenly disperse the dried wood fiber in step 1 in the reactor, while ensuring that the reactor still has a certain volume that has not been fully filled;
[0026] 3. Close the reactor, turn on the plasma generator, and adjust the working parameters of the CTP-2000K plasma power supply: the output voltage is 50V, and the output frequency is 10Hz;
[0027] 4. Surface treatment of gas medium for a period of 2-4 minutes;
[0028] 5. Control the power of the plasma generator and the temperature in the reactor to 200-240°C, and the heating rate...
specific Embodiment approach 2
[0038] Specific embodiment two: what this embodiment is different from specific embodiment one is: the reaction treatment time is 2min in the step 4, and the surface free radical content of wood fiber increases in this reaction time, and action time is short, and efficient is high, handles more fully simultaneously , The weak boundary of wood fiber and lignin surface is removed in large pieces, which makes the surface of the material undulate and rough, and the bond is broken to form free radicals. Etching has a significant effect on improving adhesion and hygroscopicity. Other steps are the same as in the first embodiment.
specific Embodiment approach 3
[0039] Specific embodiment three: the difference between this embodiment and one of specific embodiments one to four is that the gas in step six is oxygen, and the amount of oxygen entering the reactor can be controlled by controlling the size of the air inlet, thereby ensuring that the wood fiber and wood The elements can be fully treated, so that the heat treatment chamber is oxygen, without the influence of nitrides or carbides, and also avoids toxic gases produced by low-frequency ionization. wood burning. Other steps are the same as those in Embodiment 1 or 2.
PUM
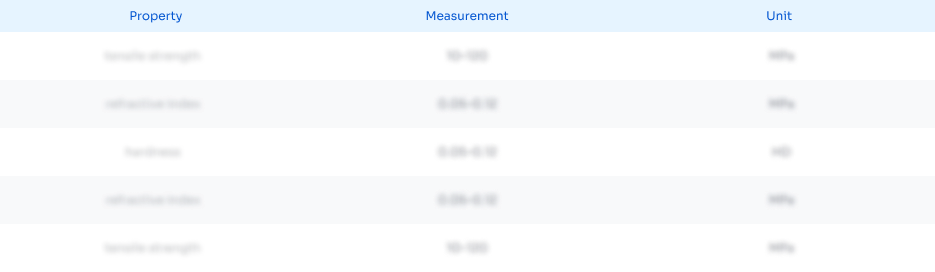
Abstract
Description
Claims
Application Information

- R&D Engineer
- R&D Manager
- IP Professional
- Industry Leading Data Capabilities
- Powerful AI technology
- Patent DNA Extraction
Browse by: Latest US Patents, China's latest patents, Technical Efficacy Thesaurus, Application Domain, Technology Topic, Popular Technical Reports.
© 2024 PatSnap. All rights reserved.Legal|Privacy policy|Modern Slavery Act Transparency Statement|Sitemap|About US| Contact US: help@patsnap.com