Lithium ion battery electrode material preparation method
A technology for lithium ion batteries and electrode materials, which is applied in the field of preparation of lithium ion battery positive electrodes, can solve the problems of inability to increase specific capacity and reduce the energy density of electrode materials, and achieve good cycle and rate performance, good cycle stability, and energy density. high effect
- Summary
- Abstract
- Description
- Claims
- Application Information
AI Technical Summary
Problems solved by technology
Method used
Image
Examples
Embodiment 1
[0040] (1) Take anhydrous aluminum chloride and sodium chloride and mix them evenly at a weight ratio of 4.6:1, and heat to 100~200℃ and stir for 10~50min to form a molten salt phase;
[0041] (2) Take 9,10-anthraquinone and pyromellitic anhydride and mix them evenly at a molar ratio of 1:1, then add them to the molten salt phase of step (1), mix well, and roast at 250°C for time. 20h.
[0042] (3) Add the calcined product in step (2) to 50 mL of 10 wt% hydrochloric acid solution, stir and acidify for 30 hours, and then filter with suction to obtain a crude product;
[0043] (4) The crude product obtained in step (3) is refluxed with deionized water, ethanol, and toluene one time in turn, each reflux time is 12-24h, and finally vacuum-dried at 60-100℃, the obtained black solid powder is For the product.
[0044] Use XRD to observe the product synthesized in Example 1, such as figure 1 Shown. From figure 1 It can be seen that there is a broad diffraction peak around 26.5°, which corr...
Embodiment 2
[0047] The difference from the above example 1 is that the raw materials in step (2) are 9,10-anthraquinone, phenazine and pyromellitic anhydride, and the molar ratio is 0.5:0.5:1 and mixed uniformly. The rest of the steps and the formula are uniform. Same as Example 1.
[0048] Use XRD to observe the product synthesized in Example 2, such as Image 6 As shown, a broad diffraction peak is observed at about 26.5° in 2θ, corresponding to the (002) crystal plane, which is a characteristic peak of carbon or graphite structure. From Figure 7 STEM image of the product and Figure 8 The nitrogen distribution map shows that the nitrogen atoms are successfully doped and the distribution is relatively uniform. Use SEM and TEM to observe the morphology of the product, such as Picture 9 with Picture 10 As shown, it can be seen from the figure that the synthesized product has a graphite-like sheet structure. Picture 11 It is the total spectrum of the X-ray photoelectron spectrum of the pr...
PUM
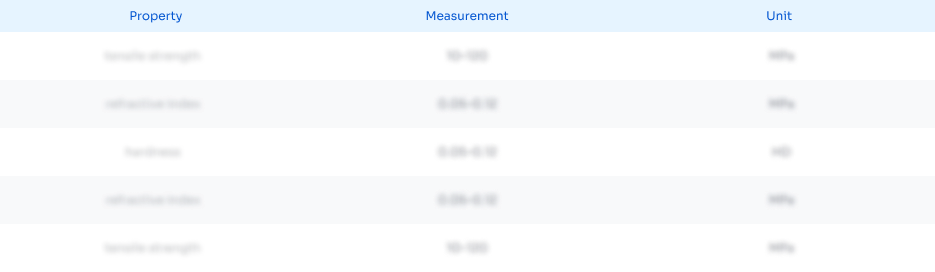
Abstract
Description
Claims
Application Information

- R&D
- Intellectual Property
- Life Sciences
- Materials
- Tech Scout
- Unparalleled Data Quality
- Higher Quality Content
- 60% Fewer Hallucinations
Browse by: Latest US Patents, China's latest patents, Technical Efficacy Thesaurus, Application Domain, Technology Topic, Popular Technical Reports.
© 2025 PatSnap. All rights reserved.Legal|Privacy policy|Modern Slavery Act Transparency Statement|Sitemap|About US| Contact US: help@patsnap.com