Method for recycling hexachlorodisilane
A technology of hexachlorodisilane and a recovery method, which is applied in the directions of halosilanes, halogenated silicon compounds, etc., can solve the problems of resource waste, hexachlorodisilane cannot be recovered, and the like, and achieve the effect of effective recovery
- Summary
- Abstract
- Description
- Claims
- Application Information
AI Technical Summary
Problems solved by technology
Method used
Image
Examples
Embodiment 1
[0043] The content of hexachlorodisilane in the polysilicon raffinate is 30%, and the treatment capacity is 3m 3 / h; filter the polysilicon residue with a basket filter with a filtration precision of 0.8 μm to obtain a colorless and transparent filtrate.
[0044] Heat the filtrate to 100°C, then pass it into the first rectification tower, control the pressure at the top of the tower to 70KPa, the temperature at the top of the tower is 100°C, the operating pressure difference is 30Kpa, the temperature at the bottom of the tower is 160°C, and the top of the tower is carried out with circulating water. Cooling, the tower kettle is heated by heat transfer oil, and the first overhead rectified liquid is obtained at the top of the tower.
[0045] Pass the distillate at the top of the first tower into the second rectification tower, control the pressure at the top of the tower to 70KPa, the temperature at the top of the tower to 100°C, the operating pressure difference to 30Kpa, and ...
Embodiment 2
[0050] The difference with embodiment 1 is that the rectification liquid in the third tower still is passed into the fourth rectification tower with a tower diameter of 0.4m. The pressure is 100KPa, the temperature at the top of the tower is 190°C, and the operating pressure difference is 50Kpa, so that the reflux ratio is 50. The top of the tower is cooled with circulating water, and the bottom of the tower is heated with heat transfer oil to obtain the fourth top distillate.
Embodiment 3
[0052] The difference with embodiment 1 is that the rectification liquid in the third tower still is passed into the tower diameter and is the fourth rectification tower of 1m, and the fourth rectification tower is a packed tower, and the packing wherein is a bulk packing, and the pressure at the top of the tower is controlled 30KPa, tower top temperature 150°C, operating differential pressure 10Kpa, so that the reflux ratio is 10, wherein, the tower top is cooled by circulating water, and the tower kettle is heated by heat conduction oil to obtain the fourth tower top distillate.
PUM
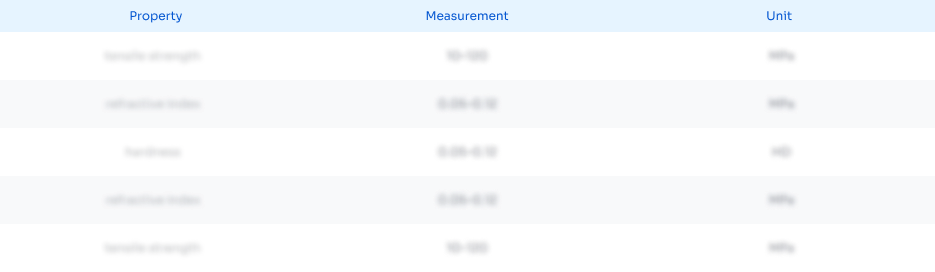
Abstract
Description
Claims
Application Information

- R&D
- Intellectual Property
- Life Sciences
- Materials
- Tech Scout
- Unparalleled Data Quality
- Higher Quality Content
- 60% Fewer Hallucinations
Browse by: Latest US Patents, China's latest patents, Technical Efficacy Thesaurus, Application Domain, Technology Topic, Popular Technical Reports.
© 2025 PatSnap. All rights reserved.Legal|Privacy policy|Modern Slavery Act Transparency Statement|Sitemap|About US| Contact US: help@patsnap.com