Energy-saving iron smelting furnace
An iron melting furnace and furnace body technology, which is applied in the field of iron and steel smelting, can solve the problems of high chimney, impact on workers' health, long payback period, etc., and achieve the effect of reducing working time, benefiting health and reducing expenses.
- Summary
- Abstract
- Description
- Claims
- Application Information
AI Technical Summary
Problems solved by technology
Method used
Image
Examples
Embodiment Construction
[0011] The following will clearly and completely describe the technical solutions in the embodiments of the present invention with reference to the accompanying drawings in the embodiments of the present invention. Obviously, the described embodiments are only some of the embodiments of the present invention, not all of them. Based on the embodiments of the present invention, all other embodiments obtained by persons of ordinary skill in the art without making creative efforts belong to the protection scope of the present invention.
[0012] see Figure 1-2 , the present invention provides a technical solution: an energy-saving iron smelting furnace, including a furnace body 5, an outer frame 1, a furnace cover 14 and a gas treatment device, the inner side of the outer frame 1 is provided with a groove frame 2 for accommodating the furnace body 5, the groove frame In order to be able to fix and accommodate the furnace body, the shape of the groove frame matches the furnace bod...
PUM
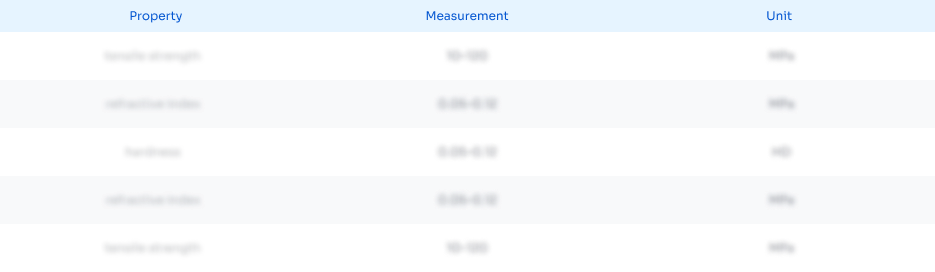
Abstract
Description
Claims
Application Information

- R&D
- Intellectual Property
- Life Sciences
- Materials
- Tech Scout
- Unparalleled Data Quality
- Higher Quality Content
- 60% Fewer Hallucinations
Browse by: Latest US Patents, China's latest patents, Technical Efficacy Thesaurus, Application Domain, Technology Topic, Popular Technical Reports.
© 2025 PatSnap. All rights reserved.Legal|Privacy policy|Modern Slavery Act Transparency Statement|Sitemap|About US| Contact US: help@patsnap.com