Method for increasing partial hydrogen pressure of hydrogenation reaction system, and design method and application thereof
A technology of hydrogenation reaction and hydrogen partial pressure, which is applied in the field of increasing the hydrogen partial pressure of the hydrogenation reaction system and increasing the hydrogen partial pressure. It can solve the problems of limiting the hydrogenation reaction depth, occupation, and unfavorable hydrogenation reaction, so as to improve the conversion of raw materials. efficiency, reduce energy consumption, and increase the yield of light oil
- Summary
- Abstract
- Description
- Claims
- Application Information
AI Technical Summary
Problems solved by technology
Method used
Image
Examples
Embodiment 1
[0030] This embodiment is a slurry bed hydrogenation process for co-refining of oil and coal. Such as figure 1 As shown, the oil-coal mixing slurry bed hydrogenation system includes two-stage reactors, that is, the primary reactor 1 and the secondary reactor 2, and the booster set between the primary reactor 1 and the secondary reactor 2 The hydrogen partial pressure separation system consists of a primary separator 3 and a gas phase separation device 4, wherein the lower end of the primary separator 3 can be a conical structure to facilitate the smooth flow of the liquid-solid phase in the separated product.
[0031] The process flow is as follows: the primary reaction product 5 obtained after the oil-coal mixture is reacted in the primary reactor 1 enters the primary separator 3 for separation, the residence time is 10 minutes, and the operating temperature and operating pressure are the same as those of the primary reactor. 1 are consistent with 450°C and 19MPa respectivel...
Embodiment 2
[0037] This embodiment is a vacuum residue slurry bed reaction process. Such as figure 2 As shown, the vacuum residue slurry bed hydrogenation system includes three reactors, that is, the first reactor 1, the second reactor 2 and the third reactor 11, and two sets of hydrogenation reactors arranged between the reactors. Partial pressure separation system: a primary separator 3 and a gas phase separation device 4 arranged between the primary reactor 1 and the secondary reactor 2, a secondary separator between the secondary reactor 2 and the tertiary reactor 11 Stage separator 12 and gas phase separation device 4. In order to save equipment, the two sets of separation systems share one gas phase separation device 4, of course, different gas phase separation devices can also be used respectively. In addition, the lower ends of the primary separator 3 and the secondary separator 12 are conical structures, which facilitate the smooth flow of the liquid-solid phase in the separat...
PUM
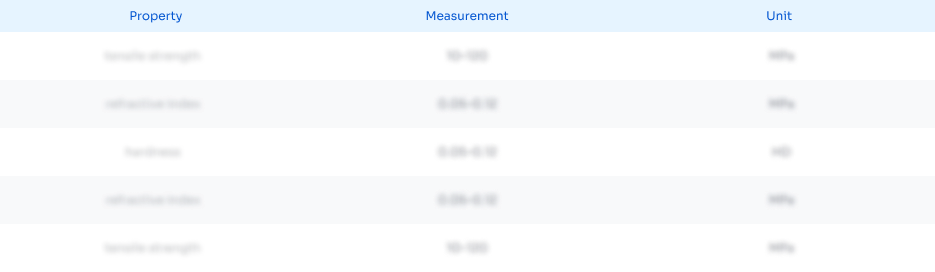
Abstract
Description
Claims
Application Information

- Generate Ideas
- Intellectual Property
- Life Sciences
- Materials
- Tech Scout
- Unparalleled Data Quality
- Higher Quality Content
- 60% Fewer Hallucinations
Browse by: Latest US Patents, China's latest patents, Technical Efficacy Thesaurus, Application Domain, Technology Topic, Popular Technical Reports.
© 2025 PatSnap. All rights reserved.Legal|Privacy policy|Modern Slavery Act Transparency Statement|Sitemap|About US| Contact US: help@patsnap.com