Pan-tilt, and control method and apparatus for pan-tilt motor
A control method and technology of a control device, applied in the field of pan/tilt, can solve the problems of complex control scheme, complex overall design, motor heating, etc., and achieve the effects of simplifying the structure design of the pan/tilt, reducing mutual influence, and reducing the total volume
- Summary
- Abstract
- Description
- Claims
- Application Information
AI Technical Summary
Problems solved by technology
Method used
Image
Examples
Embodiment 1
[0047] Embodiment 1 of the present invention provides a control method for a pan-tilt motor. The method is used to control the pan-tilt motor. The pan-tilt is a multi-axis pan-tilt, and the multi-axis is at least two axes, such as: two Axis pan / tilt, three-axis pan / tilt, etc.; each axis corresponds to a shaft motor, for example: a two-axis pan / tilt can include two shaft motors, and each shaft motor rotates around an axis (such as around the x-axis, y-axis rotation), the three-axis gimbal can include three shaft motors, and each shaft motor rotates around an axis (such as rotating around the x-axis, y-axis, and z-axis respectively); each shaft motor is composed of a corresponding rigid body member to host, for example: see figure 1 In the shown three-axis cloud platform structure, the first rigid body member 11 is used to carry the first rotating shaft motor 12, and the first rigid body member 11 is also used as a rigid body member supporting the entire cloud platform, and the ...
Embodiment 2
[0066] like image 3 As shown, the second embodiment is a three-axis cloud platform, the first rigid body member 11 is used to carry the first rotating shaft motor 12, and the first rigid body member 11 is also used as a rigid body member supporting the entire cloud platform, the first rigid body member 11 It can be fixed on the support seat, such as on the base of the drone, or on the body or head base of the ground mobile robot, or on the handle base of the gimbal of the hand-held stabilizer, etc. Two rigid body members 21 connect the first rotating shaft motor 12 and the second rotating shaft motor 22, the second rigid body member 21 is used to carry the second rotating shaft motor 22, the third rigid body member 31 connects the second rotating shaft motor 22 and the third rotating shaft motor 32, and the second rigid body member 21 connects the second rotating shaft motor 22 and the third rotating shaft motor 32. The three shaft motors 32 are connected to the carrier platf...
Embodiment 3
[0070] like Figure 4 As shown, embodiment three is a three-axis cloud platform, the first rigid body member 11 is used to carry the first rotating shaft motor 12, and the first rigid body member 11 is also used as a rigid body member supporting the entire cloud platform, the first rigid body member 11 It can be fixed on the support seat, such as on the base of the drone, or on the body or head base of the ground mobile robot, or on the handle base of the gimbal of the hand-held stabilizer, etc. Two rigid body members 21 connect the first rotating shaft motor 12 and the second rotating shaft motor 22, the second rigid body member 21 is used to carry the second rotating shaft motor 22, the third rigid body member 31 connects the second rotating shaft motor 22 and the third rotating shaft motor 32, and the second rigid body member 21 connects the second rotating shaft motor 22 and the third rotating shaft motor 32. The three shaft motors 32 are connected to the carrier platform ...
PUM
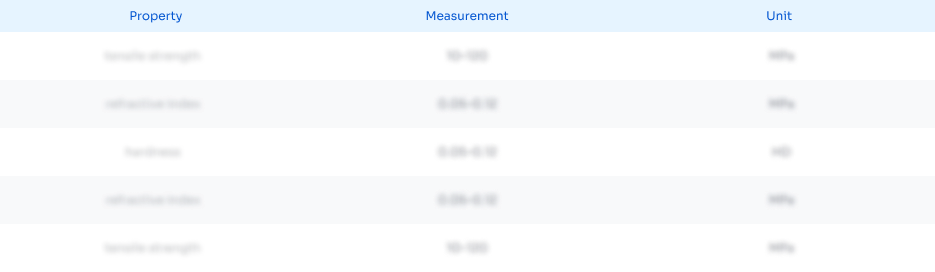
Abstract
Description
Claims
Application Information

- R&D
- Intellectual Property
- Life Sciences
- Materials
- Tech Scout
- Unparalleled Data Quality
- Higher Quality Content
- 60% Fewer Hallucinations
Browse by: Latest US Patents, China's latest patents, Technical Efficacy Thesaurus, Application Domain, Technology Topic, Popular Technical Reports.
© 2025 PatSnap. All rights reserved.Legal|Privacy policy|Modern Slavery Act Transparency Statement|Sitemap|About US| Contact US: help@patsnap.com