Horizontal casting mold and casting method for high-voltage coil of dry transformer
A technology for dry-type transformers and high-voltage coils, applied in coil manufacturing and other directions, can solve the problems of poor resin fluidity, use of standard coils, and small air-dissipating area, and achieve the effects of enhanced air-dissipation effect, cost savings, and increased contact area.
- Summary
- Abstract
- Description
- Claims
- Application Information
AI Technical Summary
Problems solved by technology
Method used
Image
Examples
Embodiment Construction
[0025] The present invention will be further described below in conjunction with accompanying drawing:
[0026] like figure 1 A horizontal casting mold for high-voltage coils of dry-type transformers is shown, which includes a coil casting inner mold 1, a coil casting outer mold 2, an end positioning and fixing support plate 3, an outer mold lining plate 4, and a terminal fixing plate 5. The inner mold 1 and the coil casting outer mold 2 are cylindrical with two ends open and they are concentric. The coil casting inner mold 1 and the coil casting outer mold 2 are placed horizontally and the two end positioning and fixing support plates 3 enclose the casting mold cavity. , the upper cylinder wall of the coil casting outer mold 2 is provided with a sprue 6, the sprue 6 is connected to the terminal fixing plate 5, and the outer mold lining plate 4 is a plate with an arc-shaped bracket 7, which is arranged on the coil casting outer mold 2 The lower end, the two end positioning fi...
PUM
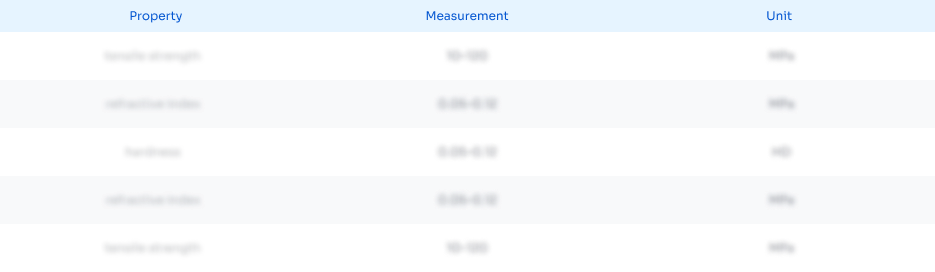
Abstract
Description
Claims
Application Information

- R&D
- Intellectual Property
- Life Sciences
- Materials
- Tech Scout
- Unparalleled Data Quality
- Higher Quality Content
- 60% Fewer Hallucinations
Browse by: Latest US Patents, China's latest patents, Technical Efficacy Thesaurus, Application Domain, Technology Topic, Popular Technical Reports.
© 2025 PatSnap. All rights reserved.Legal|Privacy policy|Modern Slavery Act Transparency Statement|Sitemap|About US| Contact US: help@patsnap.com