Production technology of all dielectric layer twisted nonmetallic optical cable
A production process and layer-twisting technology, which is applied in the field of production technology of all-dielectric layer-twisted non-metallic optical cables, can solve the problem that the number of all-dielectric cores cannot meet the requirements of use, such as the extrusion tension of figure-8 optical cables, and can increase the pressure. , the extrusion flow is uniform, the effect of increasing resistance and back pressure
- Summary
- Abstract
- Description
- Claims
- Application Information
AI Technical Summary
Problems solved by technology
Method used
Image
Examples
Embodiment 1
[0025] A production process for an all-dielectric layer stranded non-metallic optical cable, comprising:
[0026] (1) Material transmission: the cable core 3 coils and the FRP reinforcement 1 coil are transmitted through the fixed pulley, and the tension ratio of the cable core 3 coils and the FRP reinforcement 1 coil is 1.2:1;
[0027] (2) Guide mold positioning: cable core 3 and FRP reinforcement 1 are on the same vertical plane and kept parallel;
[0028] (3) Extrusion of polyethylene sheath 2: the temperature of each part of the extruder is higher than the melting point of the polyethylene material at 215°C, and the cable core 3 and FRP reinforcement 1 are formed in the extruder in a relatively tension-free state. There are double-layer filter screens in the neck of the molding machine;
[0029] (4) Cable cooling: the cooling water tank is divided into three sections for cooling, the temperatures of the first cooling, the second cooling and the third cooling are 44°C, 34°...
Embodiment 2
[0043] A production process for an all-dielectric layer stranded non-metallic optical cable, comprising:
[0044] (1) Material transmission: the cable core 3 coils and the FRP reinforcement 1 coil are transmitted through fixed pulleys, and the tension ratio of the cable core 3 coils to the FRP reinforcement 1 coil is 1.3:1;
[0045] (2) Guide mold positioning: cable core 3 and FRP reinforcement 1 are on the same vertical plane and kept parallel;
[0046] (3) Polyethylene sheath 2 extrusion: The temperature of each part of the extruder is higher than the melting point of polyethylene material at 215°C, and the cable core and FRP reinforcement are formed in the extruder in a relatively tension-free state. There are double-layer filters in the machine neck;
[0047] (4) Cable cooling: the cooling water tank is divided into three sections for cooling, the temperatures of the first cooling, the second cooling and the third cooling are 46°C, 36°C and 29°C respectively;
[0048] (5...
Embodiment 3
[0061] A production process for an all-dielectric layer stranded non-metallic optical cable, comprising:
[0062] (1) Material transmission: the cable core 3 coils and the FRP reinforcement 1 coil are transmitted through the fixed pulley, and the tension ratio of the cable core 3 coils and the FRP reinforcement 1 coil is 1.2:1;
[0063] (2) Guide mold positioning: cable core 3 and FRP reinforcement 1 are on the same vertical plane and kept parallel;
[0064] (3) Polyethylene sheath 2 extrusion: The temperature of each part of the extruder is higher than the melting point of polyethylene material at 215°C, and the cable core and FRP reinforcement are formed in the extruder in a relatively tension-free state. There are double-layer filters in the machine neck;
[0065] (4) Cable cooling: the cooling water tank is divided into three sections for cooling, the temperatures of the first cooling, the second cooling and the third cooling are 45°C, 35°C and 28°C respectively;
[0066...
PUM
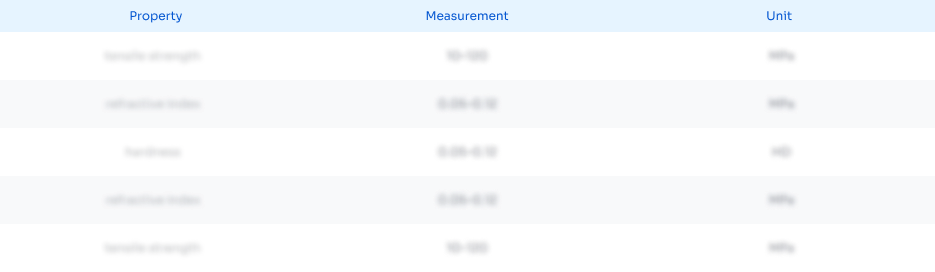
Abstract
Description
Claims
Application Information

- R&D
- Intellectual Property
- Life Sciences
- Materials
- Tech Scout
- Unparalleled Data Quality
- Higher Quality Content
- 60% Fewer Hallucinations
Browse by: Latest US Patents, China's latest patents, Technical Efficacy Thesaurus, Application Domain, Technology Topic, Popular Technical Reports.
© 2025 PatSnap. All rights reserved.Legal|Privacy policy|Modern Slavery Act Transparency Statement|Sitemap|About US| Contact US: help@patsnap.com