Highly-tenacious cut-resistant core spun yarn
A cut-resistant, core-spun yarn technology for yarn, textile and paper applications that can solve problems that affect usability, low tensile strength of steel wire or fiberglass axis, production interruptions, etc.
- Summary
- Abstract
- Description
- Claims
- Application Information
AI Technical Summary
Problems solved by technology
Method used
Image
Examples
Embodiment Construction
[0023] The present invention relates to a high-strength cut-resistant core-spun yarn, [see figure 2 , image 3 ] mainly includes:
[0024] The shaft core 1 is mainly composed of two cores of different materials, the first core wire 11 and the second core wire 12, the first core wire 11 is made of steel wire, glass fiber wire or ultra-high molecular weight polyethylene The wire, the steel wire can be a stainless steel wire, and the second core wire 12 is a wire made of para-aramid material, so that the second core wire 12 has a rougher burr surface, and on the first core A wrapping part 2 is tightly wrapped around the periphery of the wire 11 and the second core wire 12, so that the first core wire 11 and the second core wire 12 fit together and are filled in the wrapping part 2;
[0025] The wrapping part 2 is a fiber body wrapped around the shaft core part 1, and the wrapping part 2 is composed of a plurality of short fibers 21 wrapped around the first core wire 11 and the...
PUM
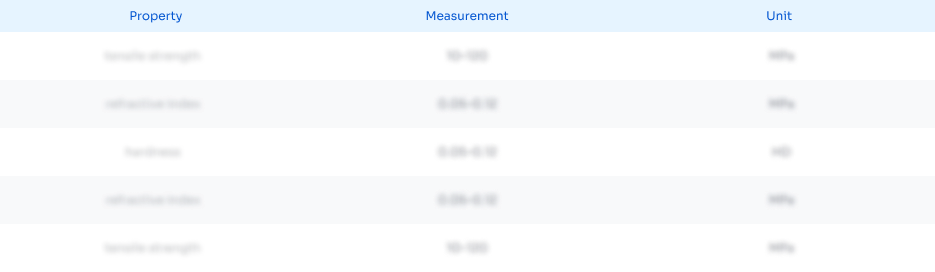
Abstract
Description
Claims
Application Information

- R&D
- Intellectual Property
- Life Sciences
- Materials
- Tech Scout
- Unparalleled Data Quality
- Higher Quality Content
- 60% Fewer Hallucinations
Browse by: Latest US Patents, China's latest patents, Technical Efficacy Thesaurus, Application Domain, Technology Topic, Popular Technical Reports.
© 2025 PatSnap. All rights reserved.Legal|Privacy policy|Modern Slavery Act Transparency Statement|Sitemap|About US| Contact US: help@patsnap.com