Industrial by-product gypsum calcining equipment
An industrial by-product gypsum and calcination technology, applied in calcium/strontium/barium compounds, inorganic chemistry, chemical instruments and methods, etc., can solve problems such as failure to achieve calcination effects, burnout of drying and calcination machines, and low temperature distribution. To achieve the effect of saving raw materials and energy, reducing output, and commissioning output
- Summary
- Abstract
- Description
- Claims
- Application Information
AI Technical Summary
Problems solved by technology
Method used
Image
Examples
Embodiment Construction
[0025] The present invention will be further described in detail below in conjunction with the accompanying drawings.
[0026] Such as figure 1 , figure 2 , image 3 , Figure 4As shown, a kind of industrial by-product gypsum calcining equipment comprises flame-breathing furnace 1, kiln head 3, drum 2, feed hopper 4, anhydrous gypsum discharge port 5, hemihydrate gypsum discharge port 6, power transmission device 8 and Waste hoist 9, the front of the drum 2 is provided with a kiln head 3, the kiln head 3 is provided with a feed hopper 4, and the drum 2 at the front of the kiln head 3 is provided with an anhydrous gypsum outlet 5 and the hemihydrate gypsum outlet 6, the anhydrous gypsum outlet 5 and the hemihydrate gypsum outlet 6 are all provided with a temperature sensor 14, the front end of the drum 2 is provided with a flame-throwing furnace 1, and the flame-throwing furnace The hot air outlet 113 of 1 corresponds to the front opening of the drum 2, and the power trans...
PUM
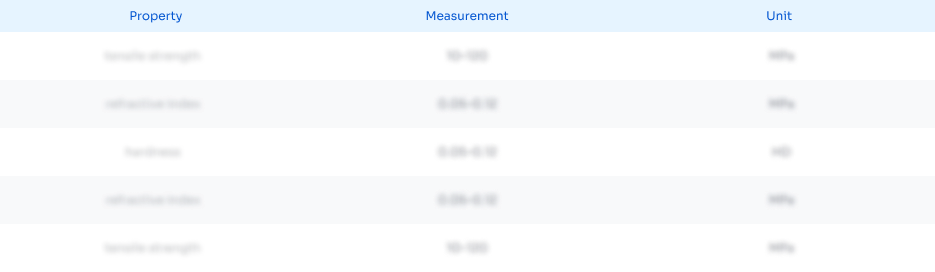
Abstract
Description
Claims
Application Information

- R&D
- Intellectual Property
- Life Sciences
- Materials
- Tech Scout
- Unparalleled Data Quality
- Higher Quality Content
- 60% Fewer Hallucinations
Browse by: Latest US Patents, China's latest patents, Technical Efficacy Thesaurus, Application Domain, Technology Topic, Popular Technical Reports.
© 2025 PatSnap. All rights reserved.Legal|Privacy policy|Modern Slavery Act Transparency Statement|Sitemap|About US| Contact US: help@patsnap.com