Plasma oxidation polishing system and method
A plasma and helium technology, applied in grinding/polishing equipment, grinding/polishing safety devices, manufacturing tools, etc., can solve problems such as difficulty in obtaining high-quality surfaces that meet optical application requirements
- Summary
- Abstract
- Description
- Claims
- Application Information
AI Technical Summary
Problems solved by technology
Method used
Image
Examples
Embodiment 1
[0023] This embodiment provides a plasma oxidation polishing system, such as figure 1 As shown, the system includes a helium tank 1. The helium tank 1 is connected to a water bottle 3 through a gas pipe, and the water bottle 3 is connected to a polishing studio through a gas pipe. The polishing studio includes a horizontally arranged rotary table 7, and a polishing block 6 is arranged on the rotary table 7. A sample 8 is placed on the upper surface of the polishing block 6, a rotating motor 5 is fixedly connected above the sample 8, an electrode 9 is also connected to the upper surface of the rotary table 7, and the rotary table 7 and the electrode 9 are respectively connected to the manual matcher 11 through wires, and the manual matcher 11. Connect the radio frequency power supply 12.
[0024] A flow meter 2 is arranged between the aforementioned helium tank 1 and the water bottle 3 . A dew point meter 4 is installed between the aforementioned water receiving bottle 3 and t...
PUM
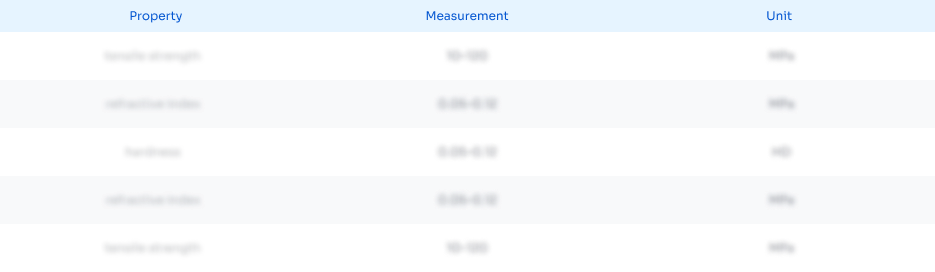
Abstract
Description
Claims
Application Information

- R&D Engineer
- R&D Manager
- IP Professional
- Industry Leading Data Capabilities
- Powerful AI technology
- Patent DNA Extraction
Browse by: Latest US Patents, China's latest patents, Technical Efficacy Thesaurus, Application Domain, Technology Topic, Popular Technical Reports.
© 2024 PatSnap. All rights reserved.Legal|Privacy policy|Modern Slavery Act Transparency Statement|Sitemap|About US| Contact US: help@patsnap.com